Chemical and plastics
Foreign metal particles are the cause of many problems in this industry. Magnets remove these often tiny metal particles and ensure that the basic properties of the raw materials remain intact.
The consequences of metal contamination
Discolouration of detergents or coatings if rust is present. They can also cause major damage in the processing of gas and oil, during combustion in a turbine or motor. Undesirable metal particles can also change the product properties. Like the conductivity of carbon black, for batteries. When fabricating plastics, unwanted metal particles reduce the insulation value of cables.
These negative effects can be avoided by applying magnets.
Magnetic filters
Magnetic filters meticulously and efficiently remove rust and small weakly magnetic metal particles our of chemicals. They help to recover ferromagnetic catalysts. This prevents damage and results in significant savings. The material choice of the magnet is particularly important. The product may be caustic and damage the seal or housing. The system must also be completely self-cleaning and be able to be used in high-pressure processes. We have developed various magnetic separators to choose from.
Carbon black
Conductive carbon black is a very dry, poorly flowing material that is used for lithium-ion and other batteries. This material can also be used for sealing and insulation materials, rubber, electrodes, paint and coatings.
It is important that carbon black is 100% metal-free, because metal particles in batteries would affect the conductivity. With magnets you guarantee the basic properties of the raw material.
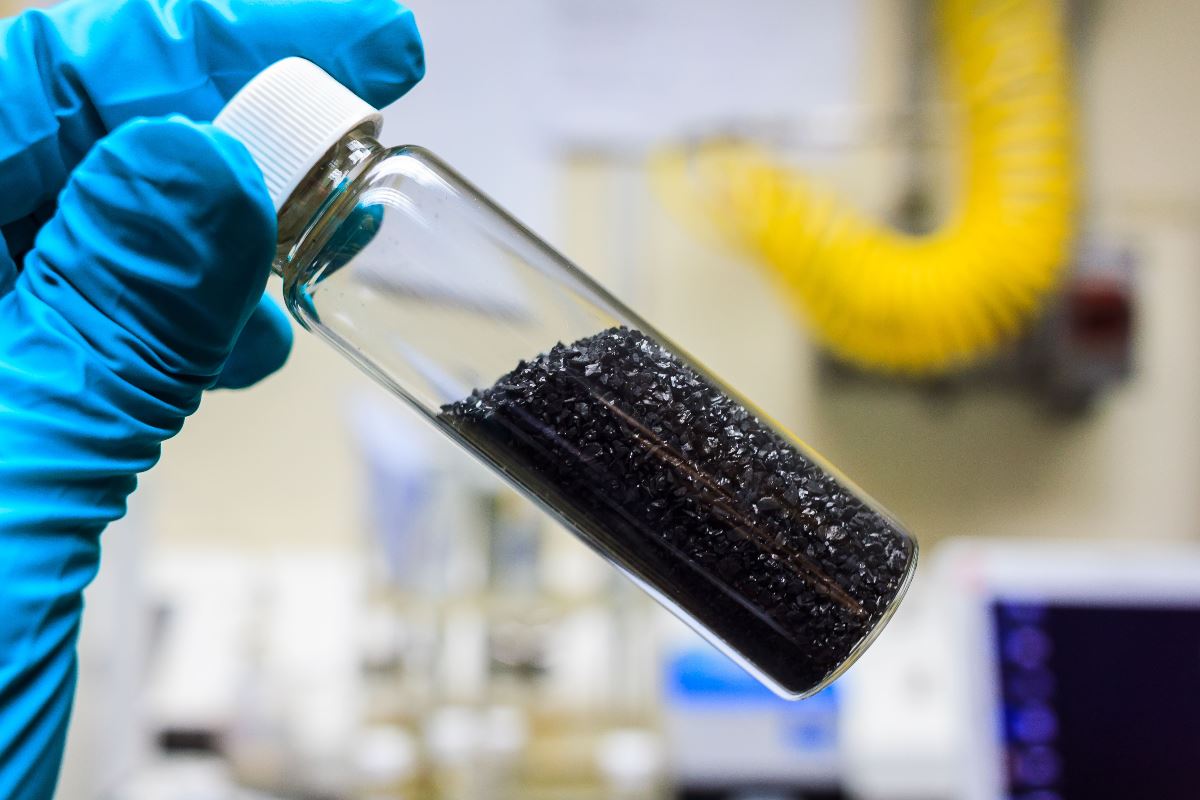
Continuous process
The production of carbon black is a continuous production process that must not be interrupted. That is why producers of, for example, lithium-ion batteries place two self-cleaning magnets in the production line.
During cleaning, which lasts 20 seconds, the product simply flows through a bypass. This means that at least one magnet is in operation during cleaning and both magnets are in use 99% of the time.
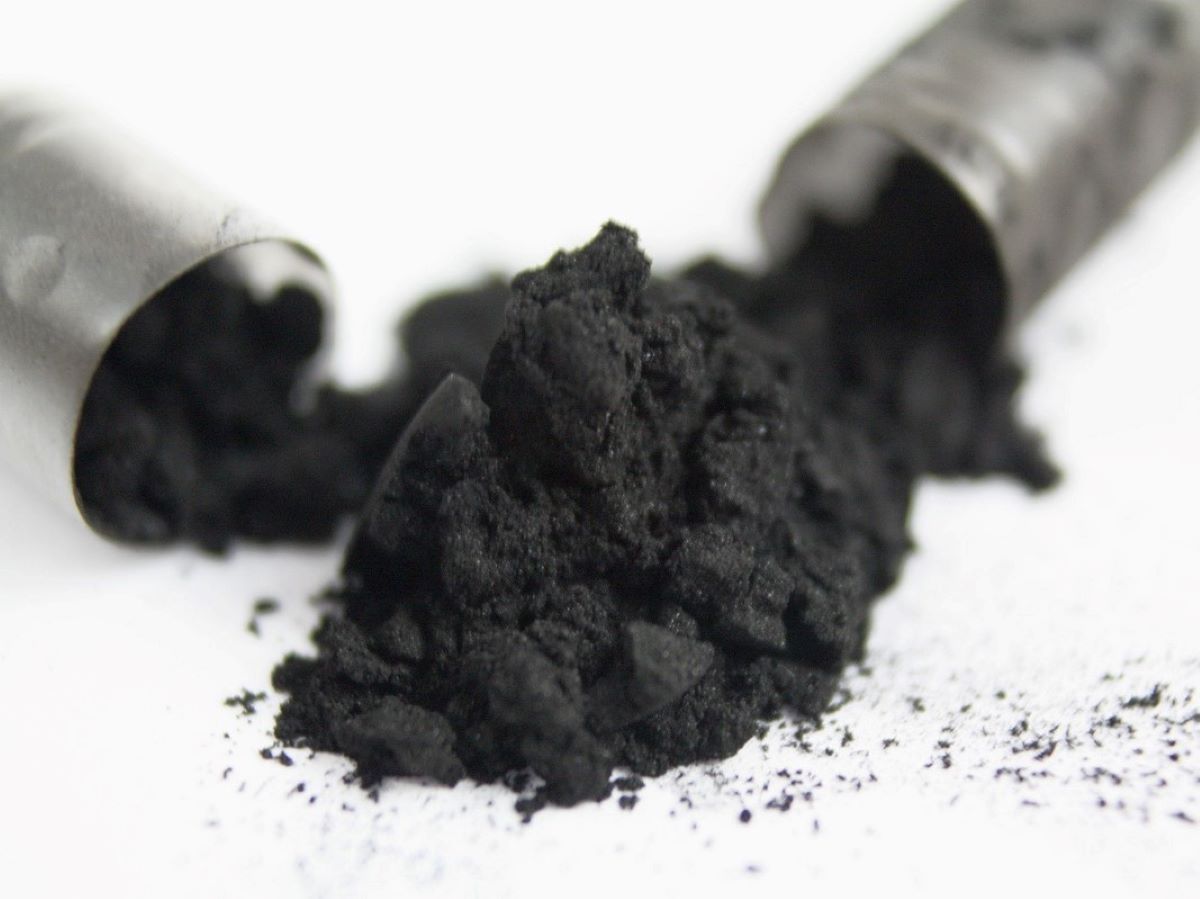
Also for poorly flowing products
These self-cleaning, rotating magnets remove iron particles from 30 µm. The rotating design ensures that the poorly flowing powder does not accumulate on the magnetic bars and they come into better contact with the material, thereby improving the separation rate.
The magnets are intended for installation in free-fall chutes. They comply with the ATEX guidelines and are resistant to a temperature of 70 °C. Higher temperature resistance is optional.
Plastic industry
Metal contamination can damage your injection moulding machines, extruders, sieves, mixers and grinders, moulds, dies or other machine components. This leads to a reduction in quality and production downtime.
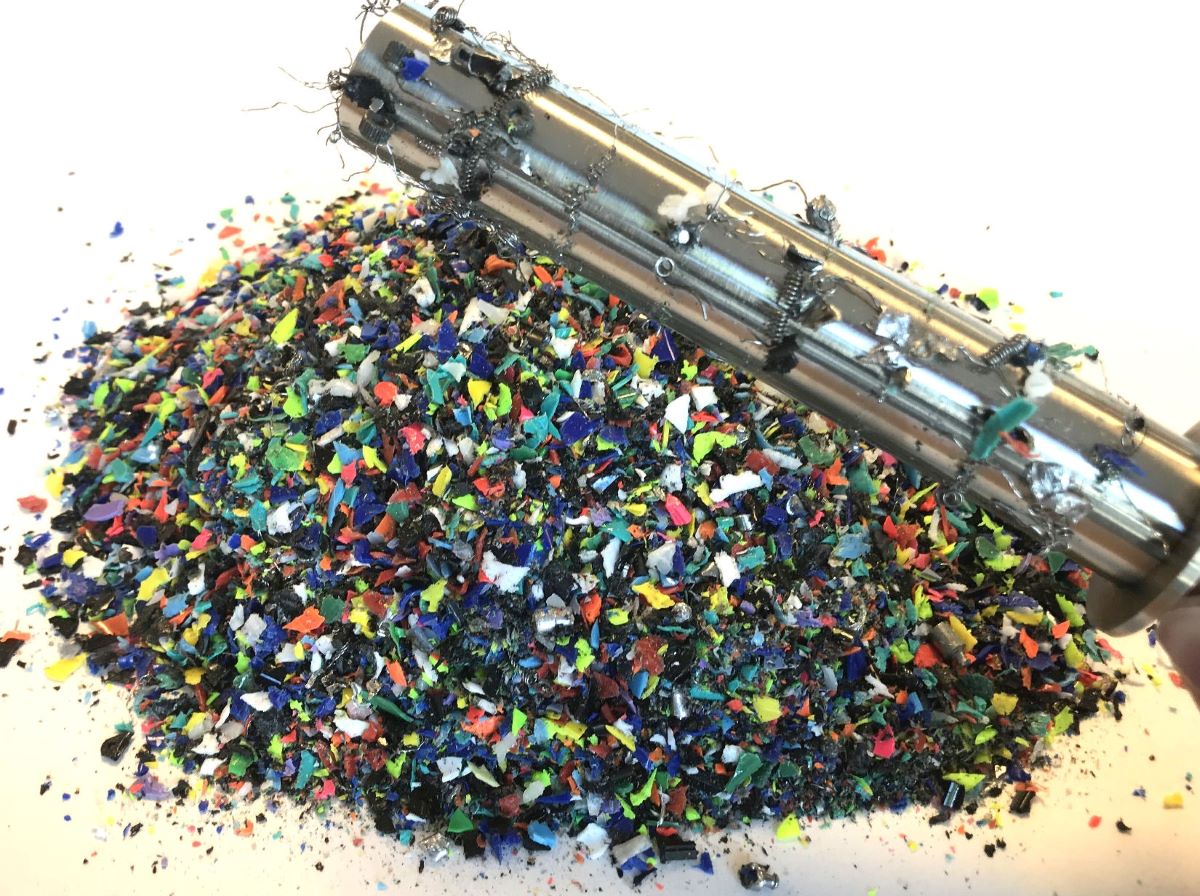
The cause of metal contamination
Plastics are supplied in granulate form, powder, or chips. This involves both recycled, as well as newly produced raw materials. It should not contain unwanted metal or foreign bodies.
The contamination can come from a variety of sources. For example, wear or damage to the machine park during the processing. Or metal particles that were already mixed in the original products in the recycled raw material and were not, or not properly removed.
The consequences of metal contamination
Possible consequences of metal contamination or foreign bodies in plastics include:
- production downtime
- machine damage
- product rejection
- undesirable product characteristics of - despite the contamination – approved products
For example, consider metal contamination in a transparent water bottle or in a pacifier: the contamination can be minor, the consequences possibly disastrous.
The Process
Injection moulding, extrusion, vacuum or pressure deformation and rotation moulding are the most common processes for plastics or thermoplastics. Unwanted metallic parts in plastics may cause clogging of the nozzle or spray openings.
Minimal nozzle thickening completely distorts the dosing of the plastic, which in the worst case scenario will result in the rejection of a whole batch of products. In addition, in the case of a blockage, the manufacturer needs to dismantle and clean the blocked nozzle or - in the worst case scenario – replace it in its entirety. This means a few hours or longer of production downtime.
In some cases, contamination does not result in a blockage of the injectors, but slips in between the pump and nozzle, and finally ends up in the finished product.
The contaminated batch is placed in quarantine for further investigation. This helps determine the cause which prevents future occurrences. In addition to the additional costs of the investigation, it may also result in a product or even entire batch being rejected.
Magnetic separation prevents damage
A magnetic filter at strategic locations in the manufacturing process not only detects contamination but immediately purifies the raw material. This prevents production downtime, machine damage, product rejection or undesired product characteristics.
Goudsmit eddy current separators are particularly well suited to plastics recycling, including PET bottles.