Static Cleanflow - automatic discontinuous
Search results
Your results in: pages, products and documents
Scroll to see everything. Didn't find what you were looking for?
Try another search term or contact us.
-
{{filter.Description}}
({{filter.UOMDescription}})
No results found
Your results in: pages, products and documents
Scroll to see everything. Didn't find what you were looking for?
Try another search term or contact us.
For high-capacity powders & granulates in chutes up to 0.5 bar
This automatic cleaning Cleanflow magnet is very suitable for situations where the magnetic separator is hardly or not accessible for operation and cleaning. Via the connection box, it is possible to connect and control the magnet via the central control room. A local control box with PLC is optional. The thick magnetic bars of Ø50 mm have a very high separation efficiency, due to a deep catch field and a high flux density. This ensures that not only ferromagnetic, but even weakly magnetic stainless steel contaminants are captured. Due to the large distance between the magnetic bars, these Easy Cleanflows have a significantly higher capacity than the Cleanflows with thinner bars. This is also an advantage for slightly less flowing powders. Suitable for granulates and reasonably to well flowing powders in free-fall and low-pressure transport pipes up to 0.5 bar.
NOT suitable for poorly flowing sticky / fatty powders that cause blockages. Rotating Cleanflows are a better solution for those applications.
Construction & materials data
Short description
These automated cleaning Cleanflow magnets contain 1 row with robust Ø50 mm magnetic bars with super strong magnet quality N52. This ensures that they optimally capture magnetic particles. In case of extremely small or weakly magnetic particles, we mount a deflector grid at the separator inlet to make sure that particles cannot fall through freely, but will touch or very closely pass a magnetic bar. The magnetic bars are sealed stainless steel tubes inside of which the magnets are blown in and out by air pressure.
Summary of important specifications
- 1 Magnetic grid with Ø50 mm robust, pneumatic operated magnetic bars.
- Optional deflector grid for guiding the product towards the magnetic bars.
- Magnet quality neodymium N-52, 12,000 gauss on the tube.
- Housing pressure-tight up to 0.5 bar.
- Material housing: AISI316(L).
- Finish: grit blasted.
- Material gaskets: Silicone EC1935 / FDA.
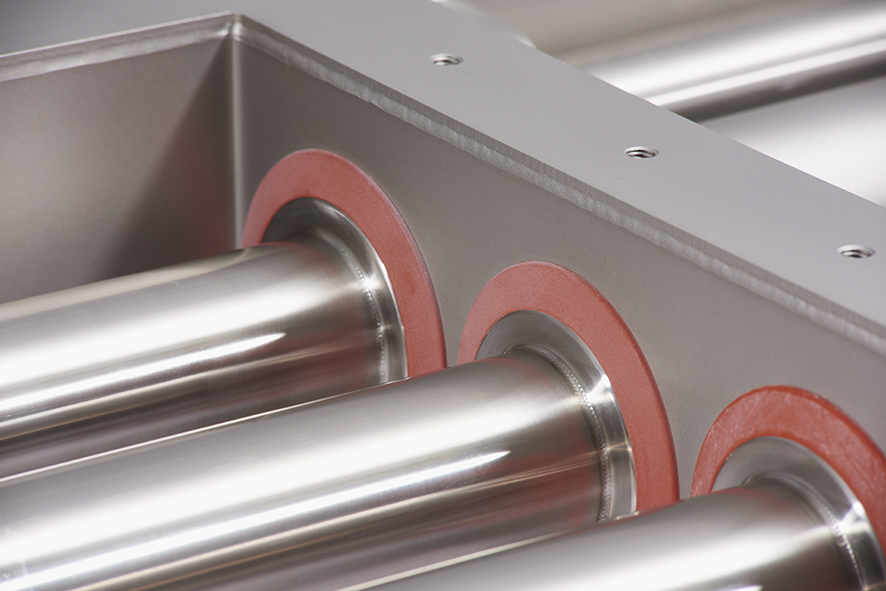
Available options
Default available options
- Inlet/outlet adapter pieces from square to round.
- High temperatures versions - to 140°C - not available in combination with ATEX.
- Removable collecting bin - for collecting discharged ferrous particles.
- Deflector grid - for guiding the product flow towards the magnet bars.
- Surface finish polishing or wet blasting - for hygienic applications.
- Flange gaskets Silicone VMQ or NBR, neutral colour, all EC1935/2004 certified.
- Alternative for red silicone VMQ housing/magnet bar gasket ring: white Silicone, blue NBR70 or black Viton FKM70 (all versions are EC1935/2004 certified).
- Thin-walled tubes - 0.7 mm instead of 1.2 mm - over the magnetic bars, for enabling catching of weakly-magnetic particles like stainless steel.
Filtering & discharging of ferrous contaminants
How does the magnetic filtering work?
The magnetic grid with very strong neodymium magnetic bars is positioned in the middle of the product flow. The product contaminated with ferrous particles passes the magnetic bars while flowing through the grid. If necessary, an optional deflector grid ensures that the product flow cannot fall freely between the magnetic bars, but is guided towards them. The magnets attract passing ferromagnetic contaminants, such as iron / steel / stainless steel wear particles. Once particles are captured they stick to the magnets, while the purified product flows further.
How does the cleaning / iron discharging work?
Each magnetic bar has a magnet package that pneumatically moves inside a closed tube, this way enabling automatic discharge of trapped ferrous particles. After the product flow has been stopped, the manual locks can be opened, after which the magnet unit must be pulled out of the product channel manually over the side guides. As soon as you pull out the magnet unit to its end of reach, air pressure automatically pushes the magnets out one stage further outside within their enclosing tubes. The moving magnets in the tubes pull the captured ferrous particles along outside. However, they are stopped by a plate halfway the tube length. As soon as the magnets have traveled completely out, the captured particles drop off the tubes, into the iron discharge chute, where you collect and further discharge them.
Cleaning / iron discharging sequence
- Stop the product stream.
- Give start signal to the magnet's control unit.
- Now first the entire magnet unit is pneumatically driven out of the product channel over a robust guide.
- Then the magnets are pneumatically moved to their OUT position within their enveloping tubes.
- The captured metal particles fall from the tubes as soon as they are outside the range of the magnetic field.
- The magnets then automatically return to their IN position and at the same time the magnet unit is driven back inside the product channel.
- As soon as magnets and magnet unit are back IN the control gives a 'ready for production' signal.
- The production can now safely be resumed.
These new 'EasyClean' type Cleanflows are equipped with robust Ø50 mm magnetic bars, that measure no less than 12,000 gauss at the contact surface of the bars. Suitable for magnetic filtering of small amounts of ferrous and even weakly-magnetic contaminants from high-capacity granulate and powder flows in free-fall and low-pressure transport pipes up to 0.5 bar. The automatic cleaning makes this separator suitable for situations where the magnetic separator is hardly or not accessible for operation and cleaning.