Metal industry
Having the right tools is half the battle. Magnets offer surprising solutions for handling and transport in the production of steel products. Magnetic tools and devices improve your production in terms of efficiency, reliability and safety.
Metal processing challenge
The market is making increasingly higher demands. Customers demand customisation with short delivery times. This requires a flexible production process that can quickly respond to changing market demand. The aim is:
- a higher yield
- faster production
- shorter delivery times
- a safe work environment.

Pneumatically operated magnet system for handling forgings
Shortage of skilled production employees
Staff shortages are also a current problem in the metal processing sector. That is why it is important to relieve your employees of physically taxing activities that do not add value. Magnetic tools and lifting magnets are very suitable for this, and provide surprising time savings.
Prevent production problems due to undesired magnetism
All kinds of production steps can cause undesired magnetism in steel products. This residual magnetism sometimes disrupts the next step of the production process. It causes problems with:
- welding of pipelines and steel structures;
- homogeneous application of surface treatments, such as uneven layer thicknesses in electrolytic coating;
- turning or milling: chips adhering to the workpiece cause surface damage.
A steel product with residual magnetism also always attracts dust. Machine parts such as cylinder rods, drive shafts and piston rings sometimes contain a residual magnetic field that attracts dust and chips. This contamination causes an accelerated wear process of moving machine parts.
With demagnetization equipment, you can reduce these unwanted magnetic fields. Our specialists can also support you on site in the case of production stagnation. With advanced equipment, they suppress undesired magnetism in the field. So your welders can get the job done again.
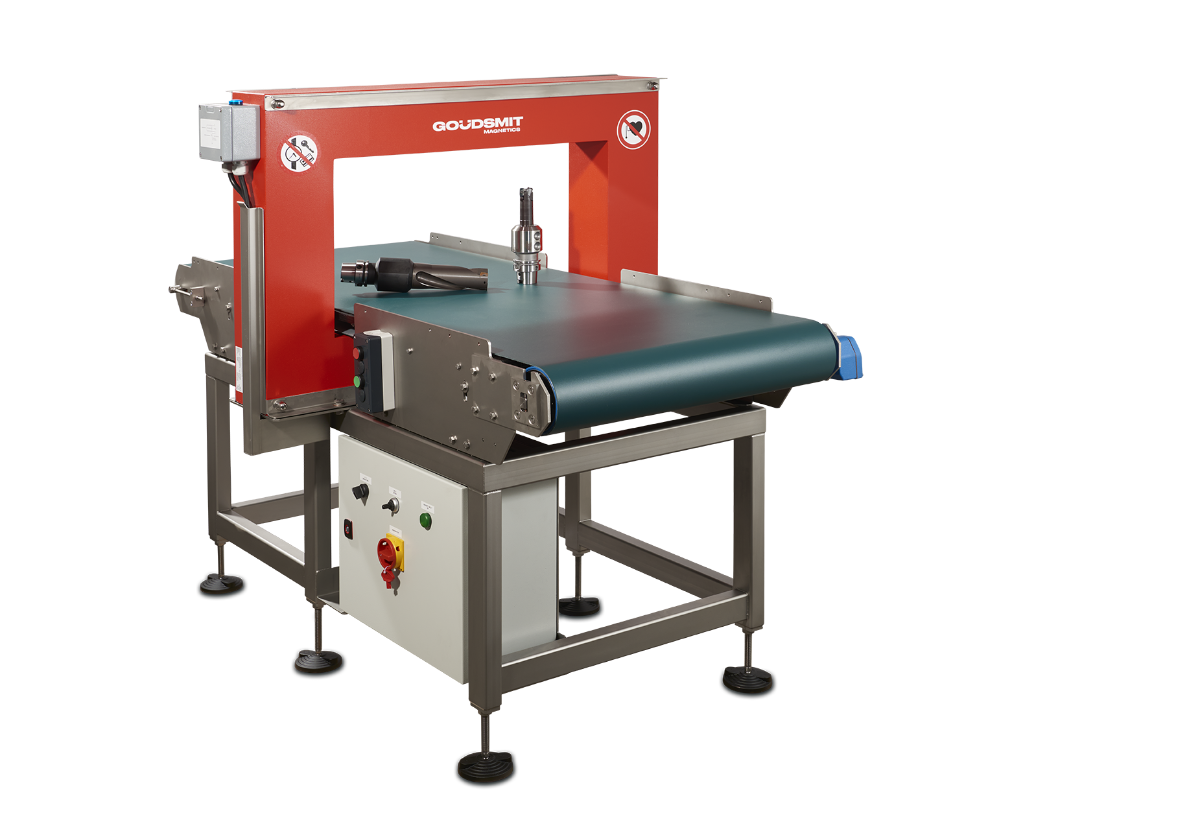
Demagnetization installation for milling tools
’Next day delivery’ and ’just in time’
Your customers prefer to be stocked within 24 hours. Meeting such delivery times requires a smooth production process, where possible through automation. This requires a production environment with machines that can be used flexibly and produce stably.
Magnet systems help you to organise the order flow as lean as possible: short changeover times and as few waiting times as possible in the process.
Man-less production
A trend in the metal industry is 24/7 production. This can be done by linking machines to robotic systems that take care of loading and unloading production machines at night. Only with reliable technology can production continue unsupervised. With the right end of arm tooling, you can produce a wide variety of products.
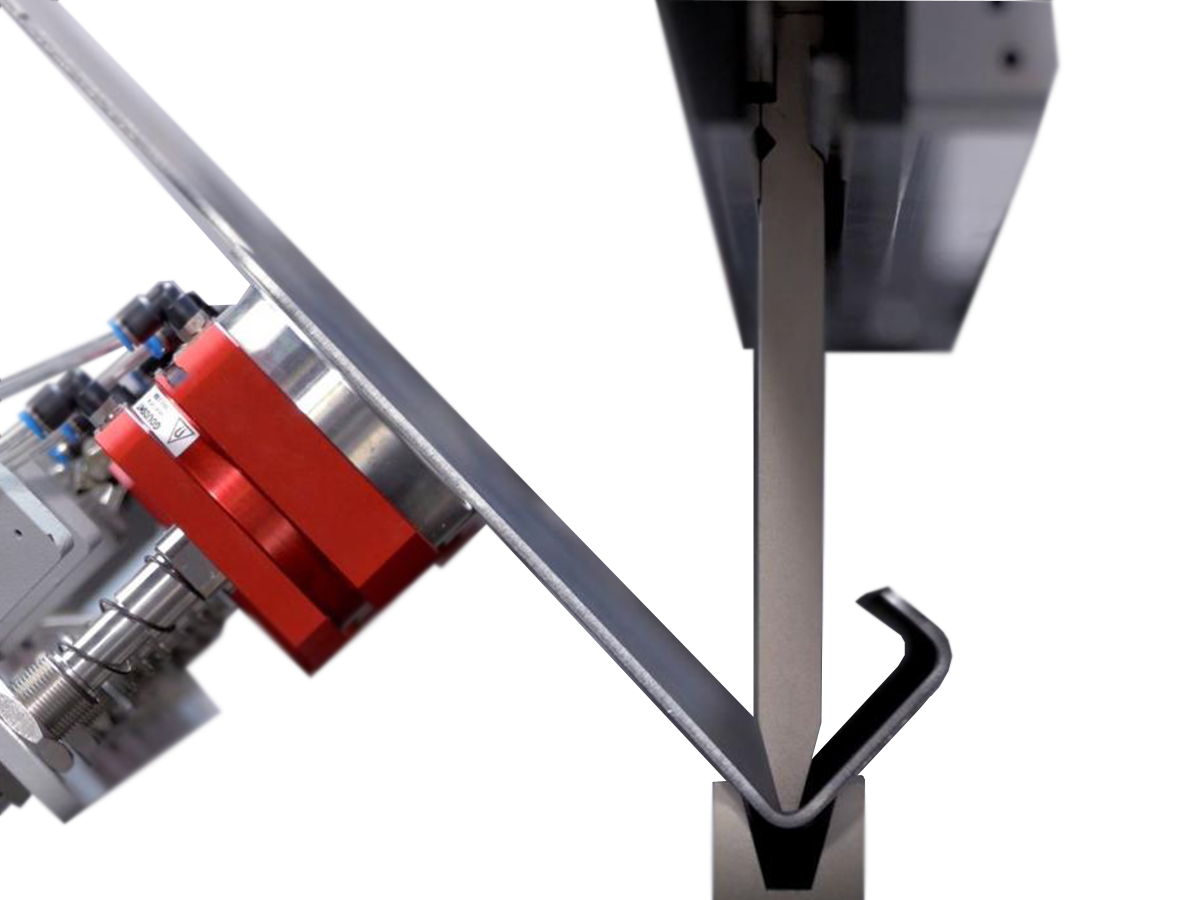
End effector magnet for robot applications
Safety and sustainability for people and machinery
Safety is always a priority in a production environment. An accident can lead to an unexpected downtime of the entire production process. The use of reliable tools and production resources is essential.
Increasingly more attention is being paid to total cost of ownership. The energy use of your production process plays a major role in this. Low power consumption and a long service life are the basis for saving the climate and minimising costs.
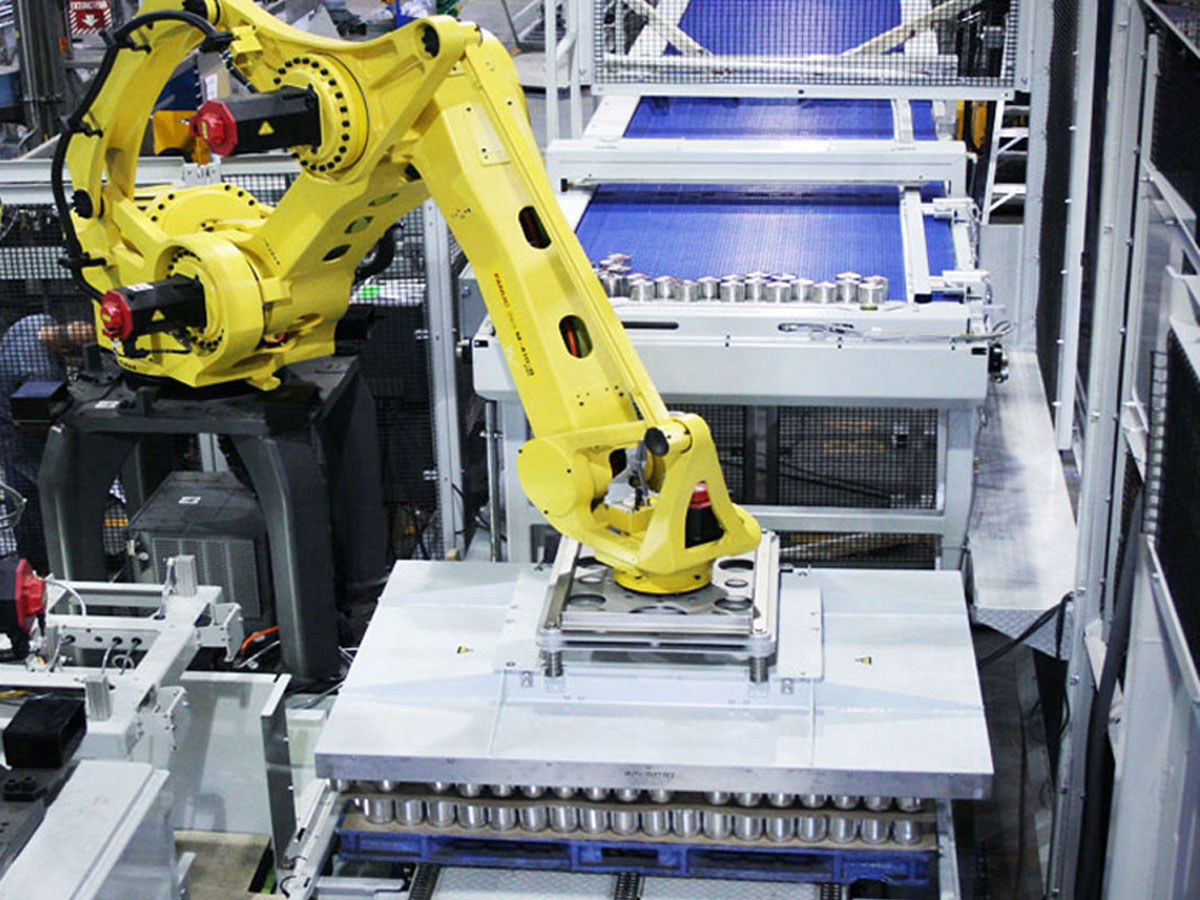
Magnetic handling of cans and glass jars with steel lids
We are happy to use our specialist skills to help you
We will gladly optimise your production environment, together with you. Thanks to many years of cooperation with our customers, our range now offers many innovative solutions for the metalware industry. We are happy to advise you on the possibilities.
Automatic loading and unloading of production machines
Robots allow you to get products in and out of the machine, which can be productive 24/7. Goudsmit has developed a sophisticated programme of magnetic end of arm tools with which your robot can accurately grip and handle metal products. These magnetic grippers meet your requirements in terms of acceleration forces, accuracy and reliability.
Integrating magnets in an automatic process
Magnets allow you to further automate the production process and speed up production. We took automation into account when designing our magnet systems. We can integrate sensors to detect the status. The magnets thus form an integral part of your fully automated production line.
Delivery from stock with a global service
When a calamity stops your production, or if you want to quickly implement an optimisation, you want a solution immediately. This is possible with our extensive range of products and parts. You can see the current stock and delivery time on this website.
We also have our own service department that is always ready to solve malfunctions or to help you install new solutions.
Magnetic grippers for automation