Lithium battery powder
Magnets play an important role in both metal recovery and battery powder purification. Magnetic separators remove metal particles from lithium powder. This prevents quality problems in the production of batteries and accumulators. To recycle lithium, magnets first remove the metal particles from the material.
Challenges in lithium processing
Metal contaminants in lithium battery powders reduce the quality and service life of batteries or accumulators. To guarantee optimum operation, perfect quality cathode powders such as nickel, manganese, cobalt oxide and lithium are required. This also applies to anode powders such as graphite, carbon black or silica.
Several years ago, a failure of one in 200,000 led to the recall of nearly six million lithium-ion packs. The manufacturer of the lithium-ion cells pointed out that microscopic metal particles can come into contact with other parts of the lithium cell, possibly leading to a short circuit. That is why magnets play a crucial role in making high-quality lithium-ion batteries and accumulators, both in the extraction and production phase. An additional challenge in the processing of lithium is its explosion sensitivity and fine grain size. Therefore, the dust density and ATEX certification of the production line is of great importance.
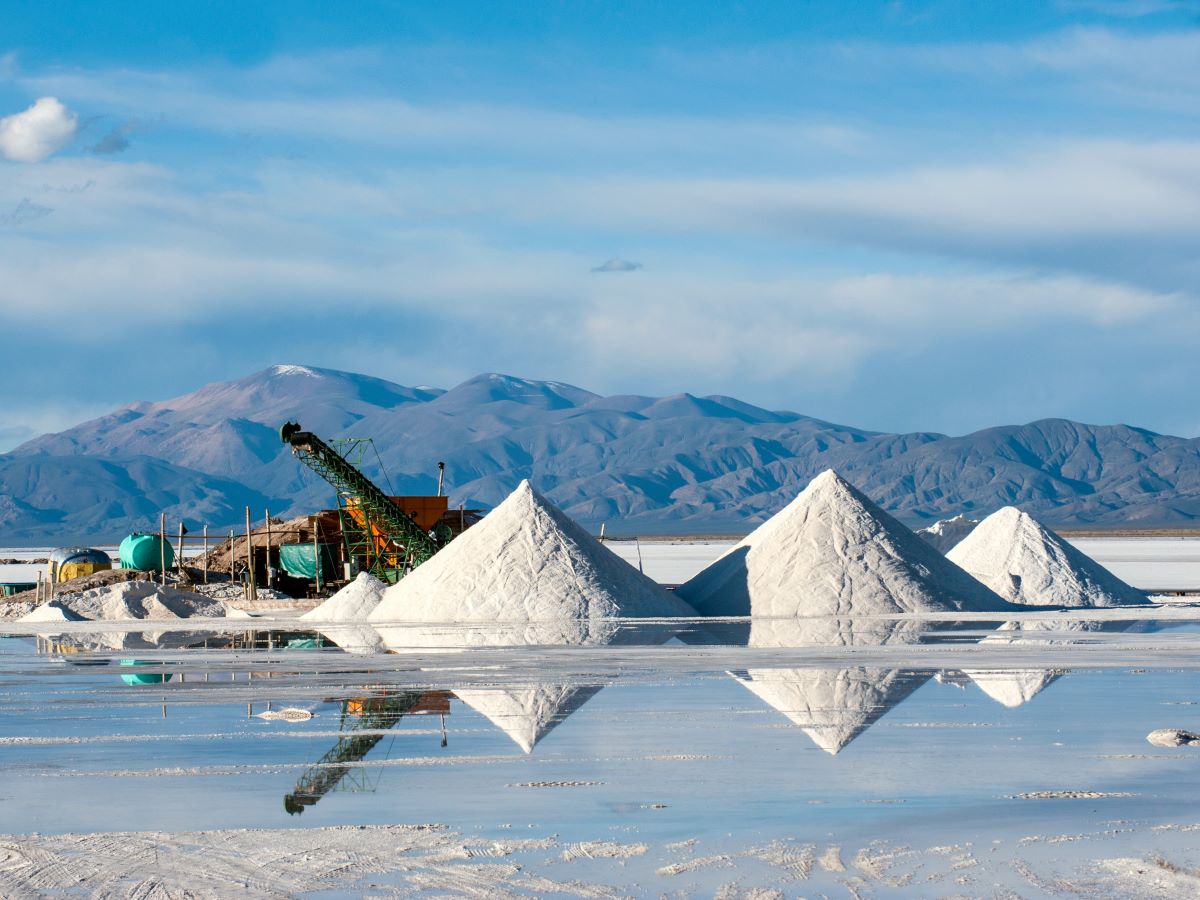
Magnetic separators ensure iron-free lithium immediately after extraction
Lithium is mined in several ways in the so-called lithium triangle of the world: Australia, Chile, Bolivia and Argentina. In Chile, this is done by extracting lithium from the salt lake of the Salar de Atacama. In Australia, lithium is extracted from solid ore. During these processes, underground brine deposits are pumped to the surface and transported to the evaporation pond. Then the water evaporates and the salt is removed. These steps are repeated a few times, until lithium carbonate remains. Plans are also in the making in Europe for the extraction of lithium from the Massif Central in France.
The result is the raw material for lithium production. Iron pollution sometimes ends up in the raw material during this process. The powder is also subject to iron pollution during subsequent transport by train and freight ship, for instance. You want to carefully filter iron particles, or nuts and bolts that contaminate the powder after transport, in order to prevent the risk of explosion. Goudsmit supplies various ferro separators that remove iron pollution from raw material flows such as lithium. These strong magnetic separators withstand the abrasive and corrosive properties of lithium powder. This powder damages the stainless steel mixers, sieves and transport spirals, and iron particles end up in the lithium powder.
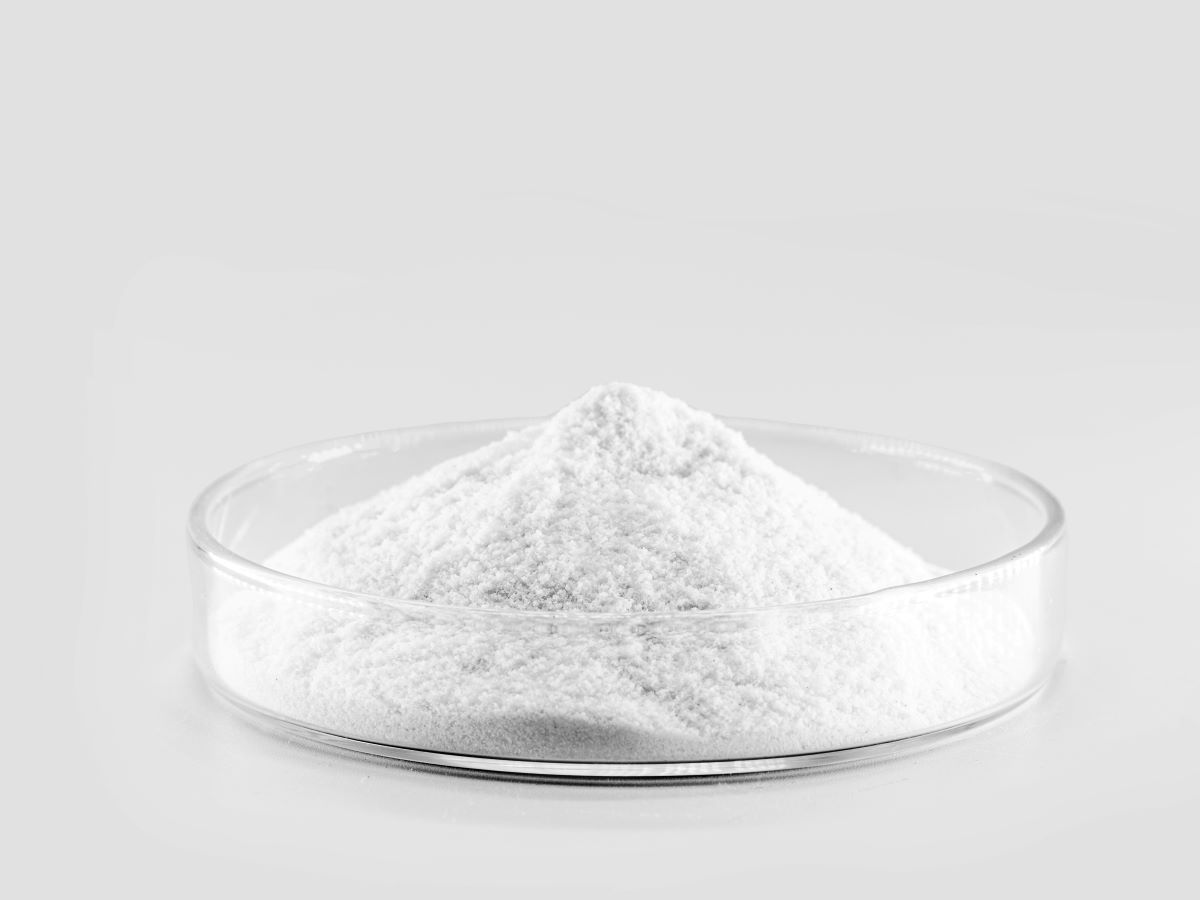
Prevent material build-up with rotating magnetic separators
The very small grain size of lithium causes, among other things, the product to flow poorly. In most cases, material build-up and bridging occurs on any obstruction in the flow. Also on the magnetic bars. Bridging not only blocks the flow, it also causes poor separation efficiency because the magnetic contaminants are diverted away from the bars.
By rotating the magnetic bars, we prevent fine powders from sticking to the bars, so that contact with the magnetic bars remains optimal. This is important because the very small and often weakly magnetic particles have to hit the magnetic bars in order to be able to ‘catch’ them. Goudsmit’s magnetic separator for lithium contains nine large, extra strong magnetic bars. These pneumatically operated magnetic bars with a diameter of 50 mm have a deep holding field. With a flux density of 12,000 gauss on the bars, the magnet can capture paramagnetic particles in addition to iron particles.
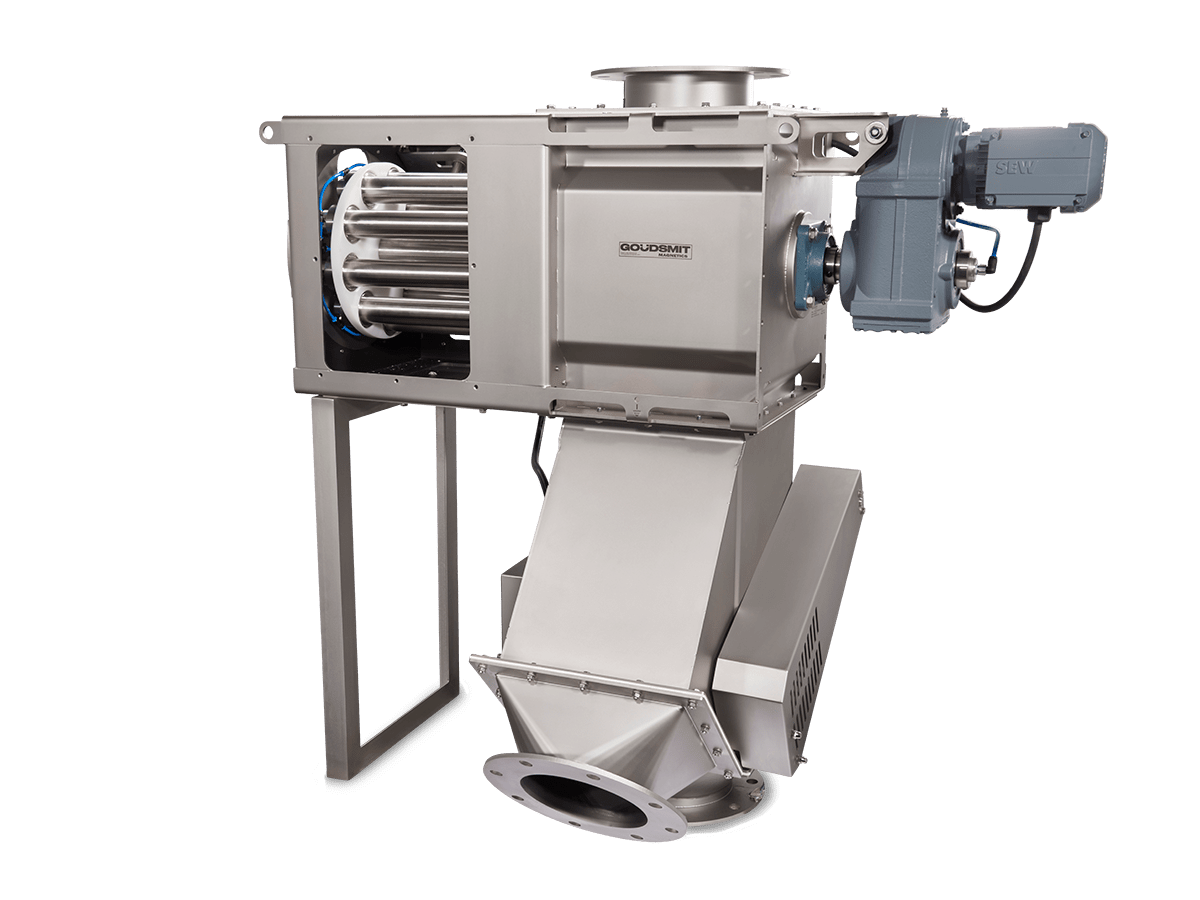
Purifying powders for lithium-ion battery production
As the battery market grows globally due to the increasing demand for batteries for laptops, telephones and electric cars, among others, battery manufacturers are under pressure to improve battery performance, reduce their environmental footprint and reduce costs. Battery users want faster charging, higher charging capacity and longer battery life. At the same time, manufacturers want more compact batteries with a higher energy density, reliability and a safe production process. In the coming years, the market for recycling lithium batteries and battery packs will grow enormously, due to the ambitions of leading car manufacturers to reduce the waste flow. The aim is to achieve a 100% closed-loop system by optimising the recycling process, without any waste flow.
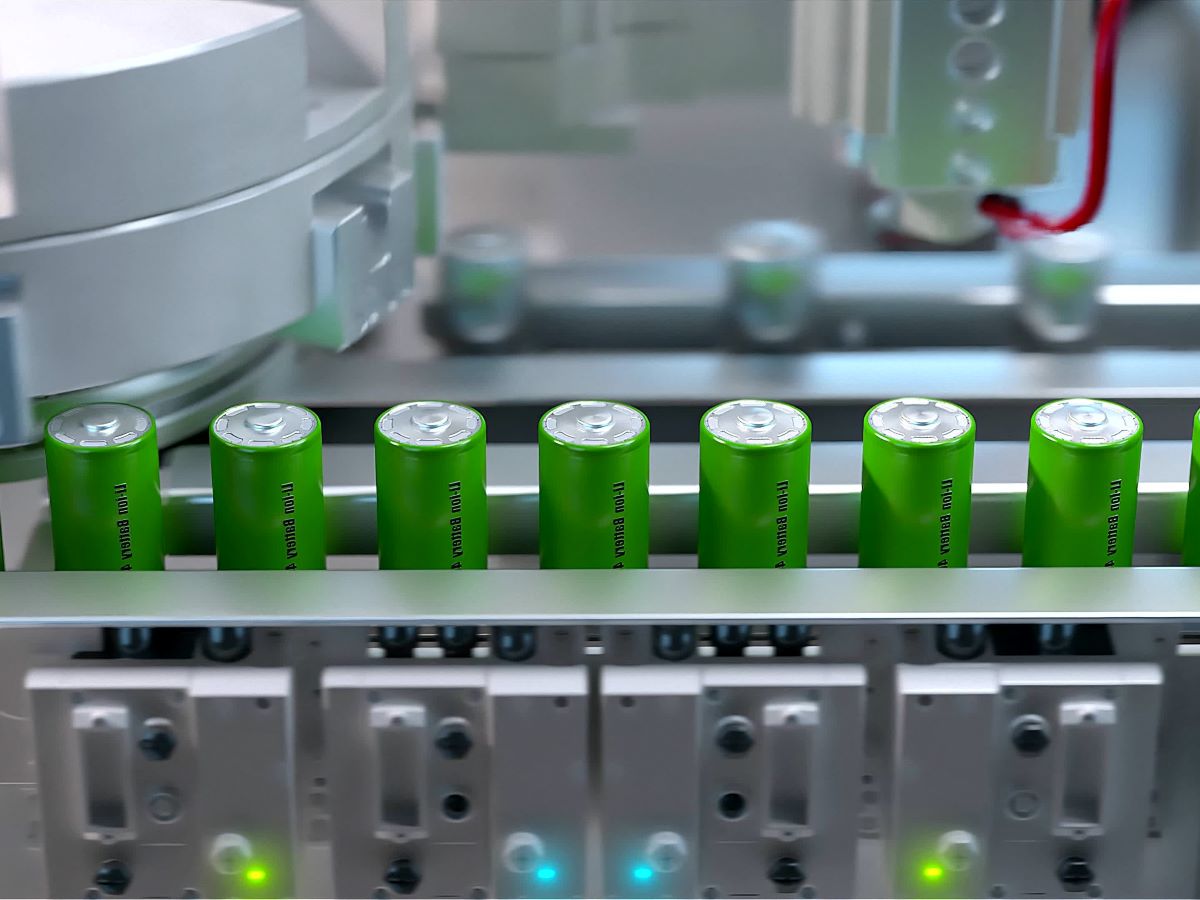
A sustainable future with a leading role for lithium recycling
The use of lithium is not very sustainable yet. This is due to the fact that the recycling chains are not optimally developed and no scaling-up has taken place. However, lithium itself does have the potential to contribute to the storage of green energy. This will make us less dependent on fossil fuels. Due to the rising demand for lithium and the expected shortages in the global market in the coming years, battery recycling is of great importance. The challenge in the battery recycling process is in separating valuable materials such as lithium, cobalt and nickel.
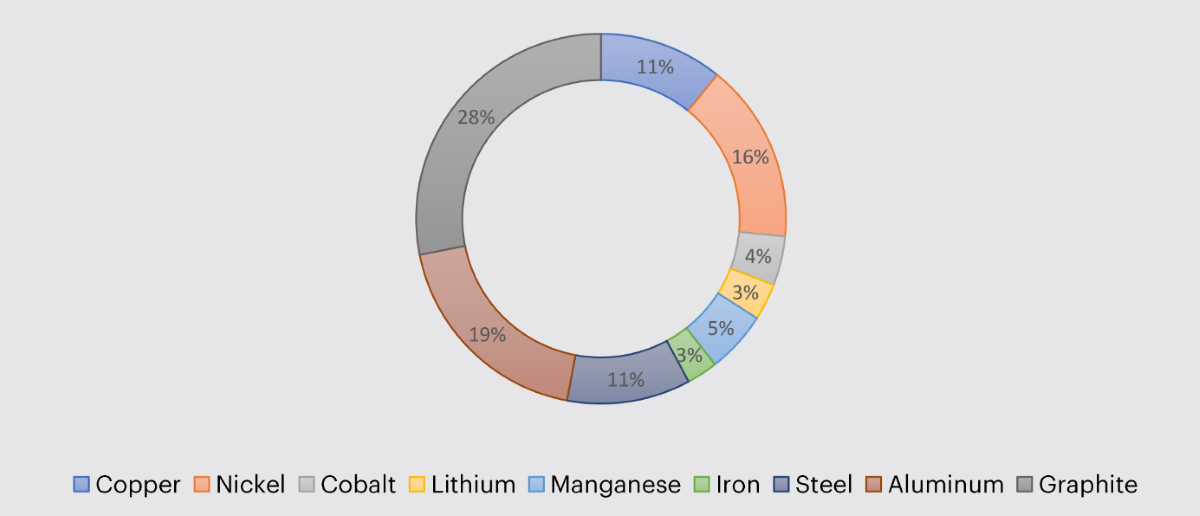
Valuable minerals in lithium-ion batteries
Traditionally, many batteries with high cobalt contents are recycled pyrometallurgically (smelting) to recover the valuable cobalt. In modern battery technologies, however, increasingly less cobalt is used, and the focus is on recovering the valuable lithium. Magnets play an important role in the mechanical part of the recycling process, prior to hydrometallurgy (dissolving in acids). After shredding, the shredded material is screened and magnetically separated. The residual flow is then washed and undergoes heat treatment before entering the chemical process. With hydrometallurgical recycling, it is possible to achieve a result of up to 99.6% clean Li, Co, Ni raffinate. You can also recover copper, manganese, iron and aluminium with this method. After the chemical separation of minerals, the Li, Co, Ni raffinate can be filtered magnetically. So, you are only left with pure, non-magnetic lithium.
Currently, this process is less attractive compared to the relatively low costs of lithium mining. However, recycling technologies are improving rapidly, which allows this industry to complement mining. In this way, it contributes to making the value chain more sustainable in automotive and consumer electronics, among others.
.png)
Customer-specific testing for an optimal result
Due to the complexity of battery production, finding the right solution can be a big quest. That is why Goudsmit believes in conducting customer tests with your specific product flow. We first determine what your needs are and what options we have for this. We collaborate in the entire process and provide sound advice with the help of FEM magnet calculations if necessary. This way you know exactly where you stand and which magnet solution fits your purification or recycling needs.
We are looking for partners in the ever-developing lithium industry
Since the lithium market is fully in development, we would like to enter into cooperation with companies that are active in lithium processing. We are keen to contribute to the development of the best magnetic separation technology for battery powders with our innovative magnet solutions. We are keen to develop, together with you, a magnetic separator that meets all your requirements and that ultimately sets the tone for a completely new industry standard.