Food industry
The consequences of undesired metal particles in food production processes are often unclear: from machine damage and production downtime to rejection of products and damage claims. We help food producers ensure food safety and quality processes.
Food manufacturing challenges
Populations and prosperity continue to grow worldwide. This will also increase the need for high-quality food. The food and beverage industry is meeting this need. Plants small and large produce food for the local population or for export. As a food manufacturer, you want stable output from your food production so you can meet the constant demand for products.
Prevent food contamination and recalls
One of the biggest challenges in the food industry is safeguarding food safety. You want to avoid at any costs involved in product contaminants such as foreign bodies or bacterial growth. This is because it leads to rejection or large-scale recalls, which ultimately lead to high costs and reputational damage.
Metal pollution and bacterial growth in product channels or pipelines
Foreign bodies, in the form of metal contamination, end up in food products through:
- contaminated material input
- machine wear and tear
- maintenance of the production line
Metal pollution occurs from large parts measuring >50 mm, such as bolts and nuts, to very small metal particles of 30 µm.
Bacterial growth in the product channel can occur with surfaces, gaskets or transitions that are difficult to clean. Properly cleanable machines with good product flow and food-safe parts are therefore essential.
Capture iron and stainless steel contamination efficiently with a magnet
There are many types of magnetic separators, but choosing the wrong type results in too low separation efficiency. Parameters such as viscosity, type of metal pollution, density, humidity, pressure and temperature are crucial for determining the right magnetic separator for your specific process.
Guaranteeing consistent quality and output
A production line with consistent quality and output is a second major challenge. All kinds of influences can cause machines to perform poorly. This also applies to the magnets in your production line.
If a product becomes too hot or damages magnets, the separation efficiency or magnetic force may decrease. That is why it is important to have your magnets inspected frequently. This allows you to validate whether the magnets are still performing properly so that you continue to meet the international food safety standards such as HACCP and EHEDG.
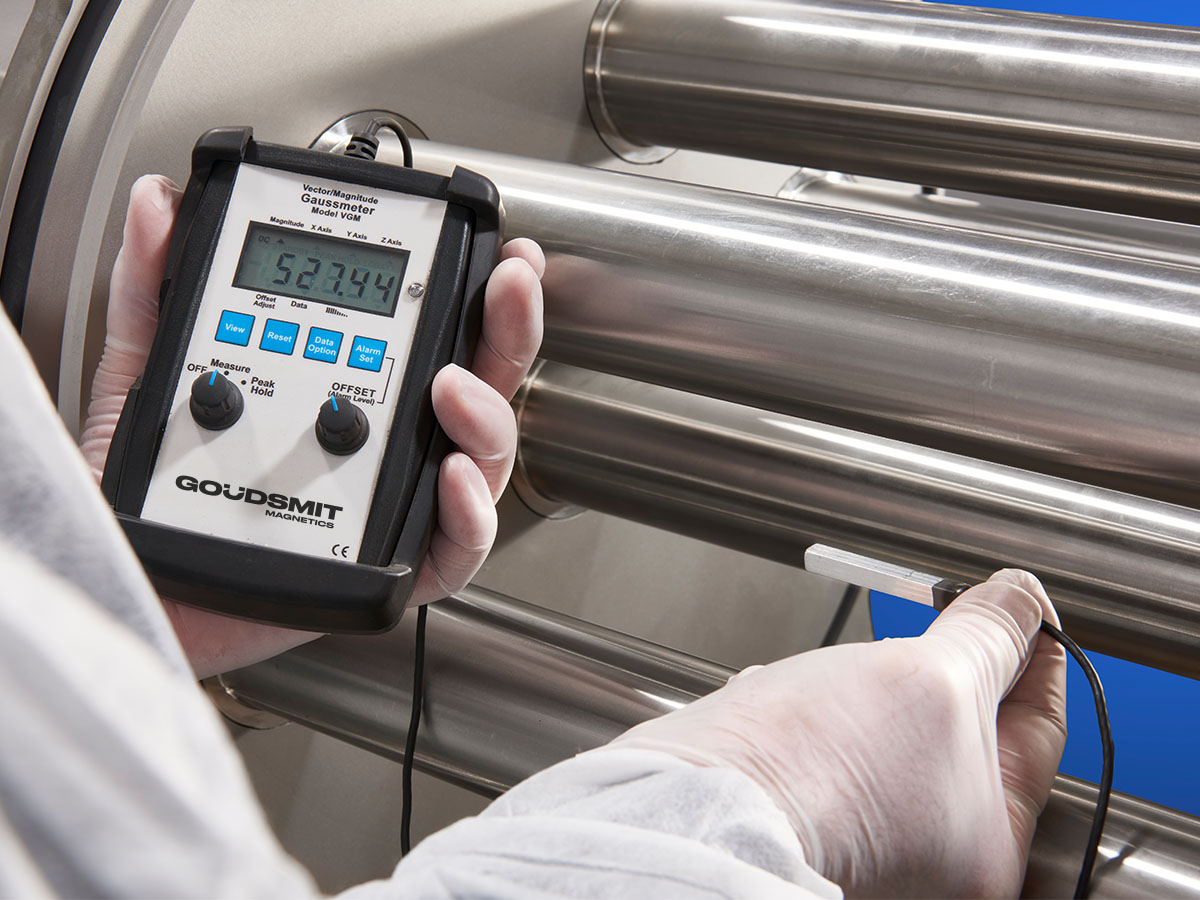
Magnet inspection with 3D gaussmeter
We are happy to use our specialist skills to help you
Goudsmit develops and produces magnet systems for the separation of iron and stainless steel from food products. By working with leading food manufacturers and partners, we have gained a lot of practical knowledge. We are happy to share our insights and help you with solid solutions to your specific problem.
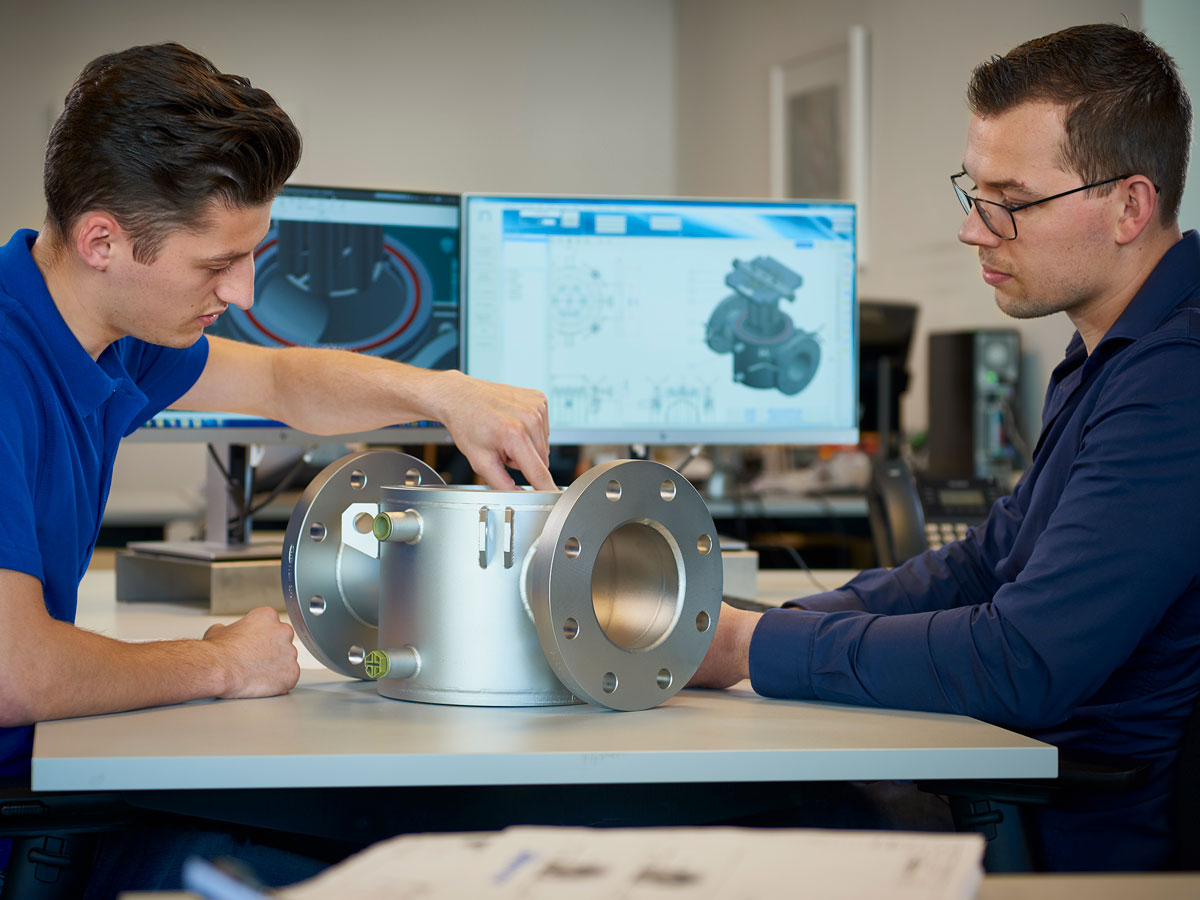
Magnetic engineering design
Highest separation efficiency through 3D simulations
Magnet calculations and simulations are the basis for designing efficient magnet systems. Our simulation engineers predict magnetic performance accurately based on application and usage.
With these simulations, our design engineers develop the best magnetic separators. This ensures that magnet performance, finishing, capacity and cleaning capabilities are perfectly aligned.
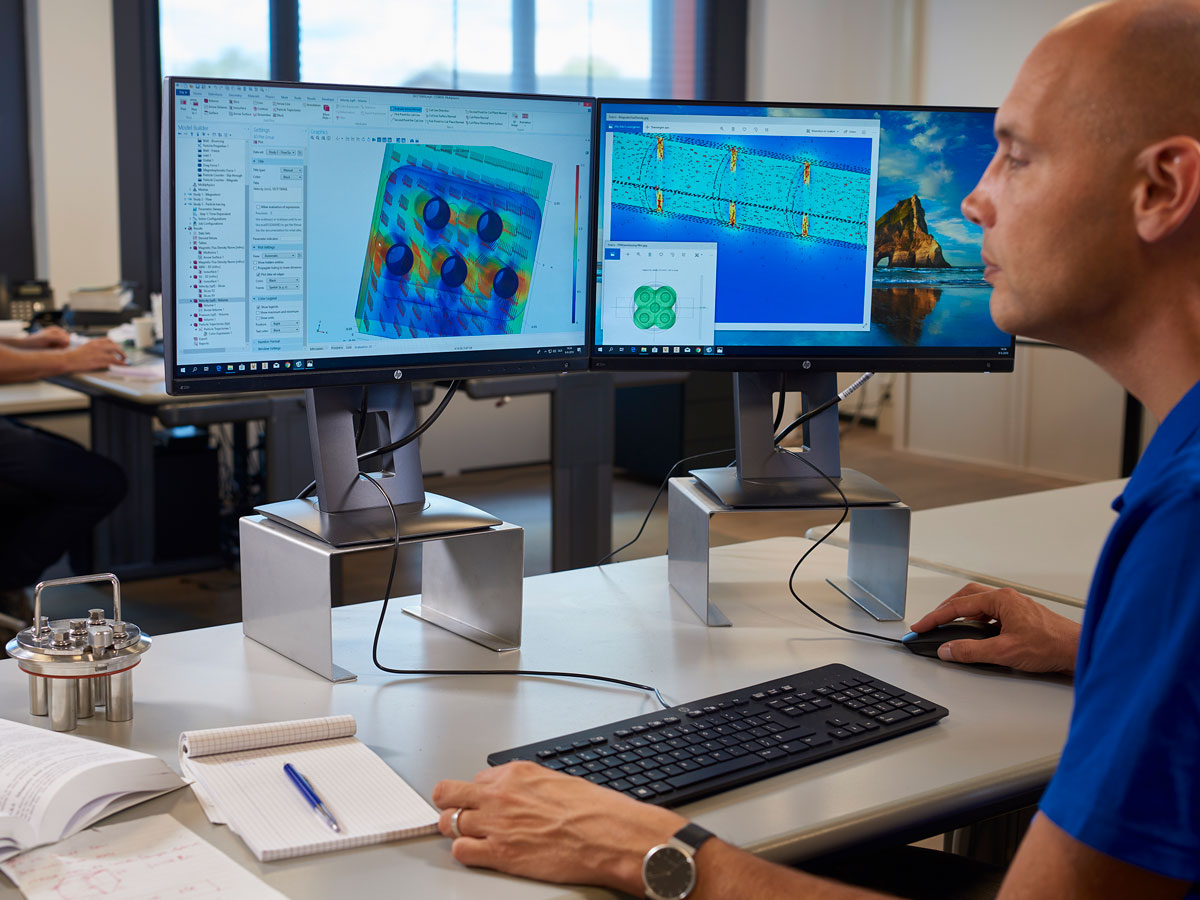
Magnetic flow simulation
No contamination due to hygienic EHEDG design
Many Goudsmit magnetic separators are EHEDG-certified. The EHEDG consortium sets the standard for the safe and high-quality production of foodstuffs. The independent consortium is authorised to certify products when they meet this standard.
If you choose one of our EHEDG-certified products, you can be sure that it meets the highest hygienic standards with the best finish. This solves the problem of food contamination in your magnetic separator.
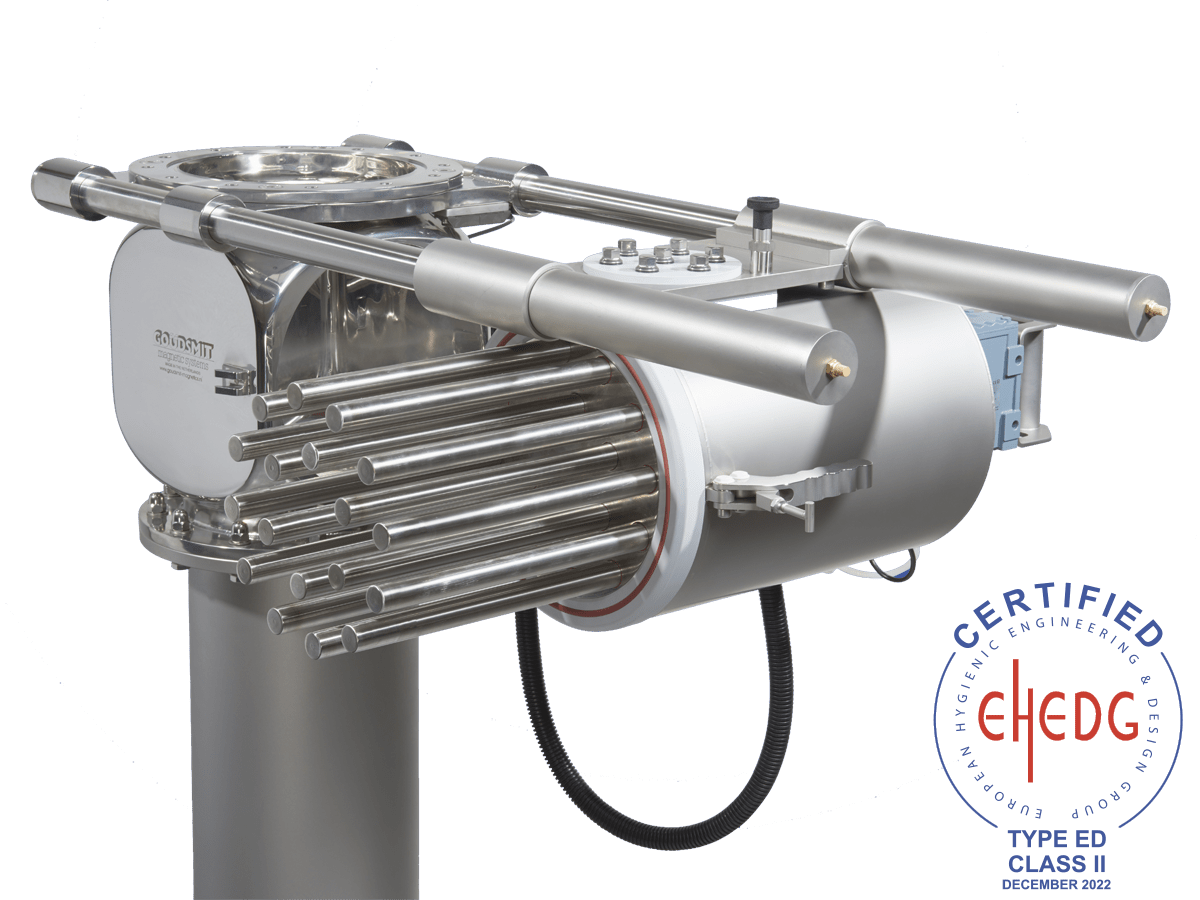
EHEDG hygienic Cleanflow magnet
The best finish with an HDN-certified welding department
Magnetic separators are manufactured in the company's own factory. This ensures the quality that we deliver. An important component of quality assurance is that our welders and welding robots are hygienically HDN/PED-certified.
The ‘Hygienic Design Network’ is a partnership between companies in the food industry. It establishes guidelines and standards to prevent problems in food production.
Goudsmit's welding department meets these standards and produces the highest quality and finishes in the area of hygienic and pressure-resistant welding components.
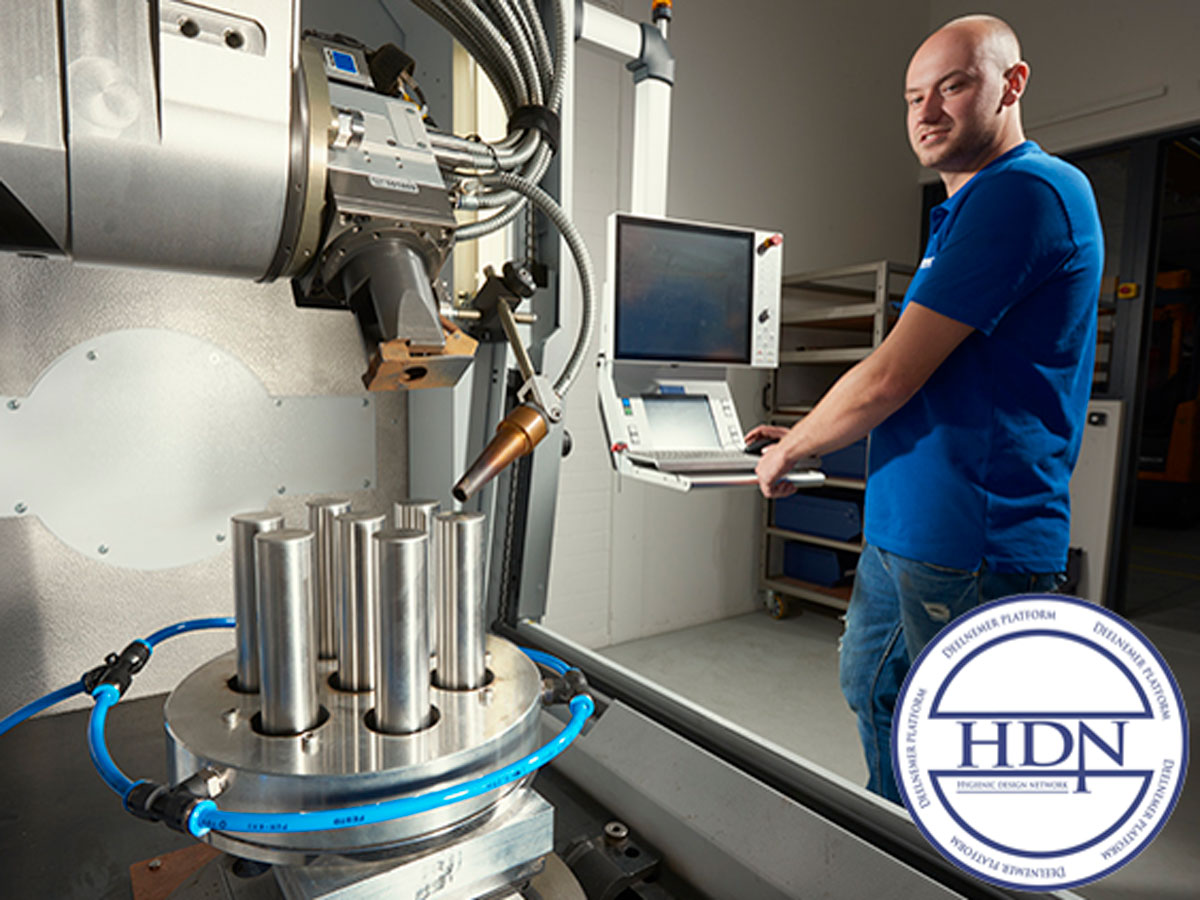
HDN certified laser welding
Leading magnetic separators for iron and stainless steel
The highest separation efficiency, the best hygienic finish and simple cleaning options ensure unrivalled magnetic separators for the food industry. With a complete range of standard or customer-specific magnetic separators, we always have a solution for your metal separation issues.
Thanks to many practical tests at the test centre with different powders, pastes and liquids, we know what works and what doesn’t. Our expert advisers are happy to help you with your production process so that we can take all the options we can offer to select the best separation solution for you.
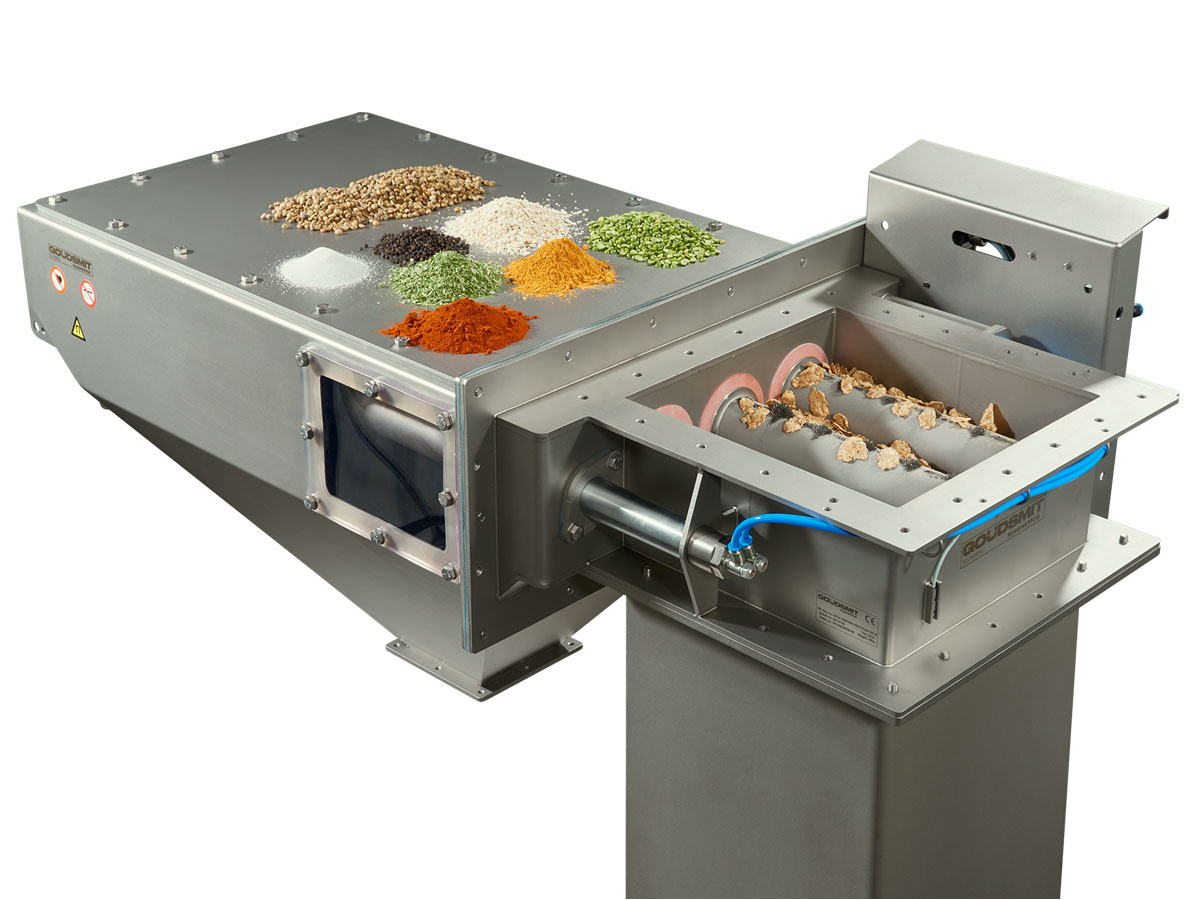
Easy Cleanflow magnet for powders and granulates
Validated magnet systems through service inspections
If you already have Goudsmit magnetic separators or another brand, we are happy to help you with the validation of your separation systems.
Our service engineers know exactly where and how to measure and carry out on-site inspections with a calibrated gauss meter. They ensure minimal interruption of your production processes and control all magnet systems at critical points. Afterwards you will receive an inspection certificate, with possible recommendations for process optimisation. This guarantees a consistent quality of your production process and product output.
Would you like more information? Read the blog: Food industry: why do you have to measure magnets?
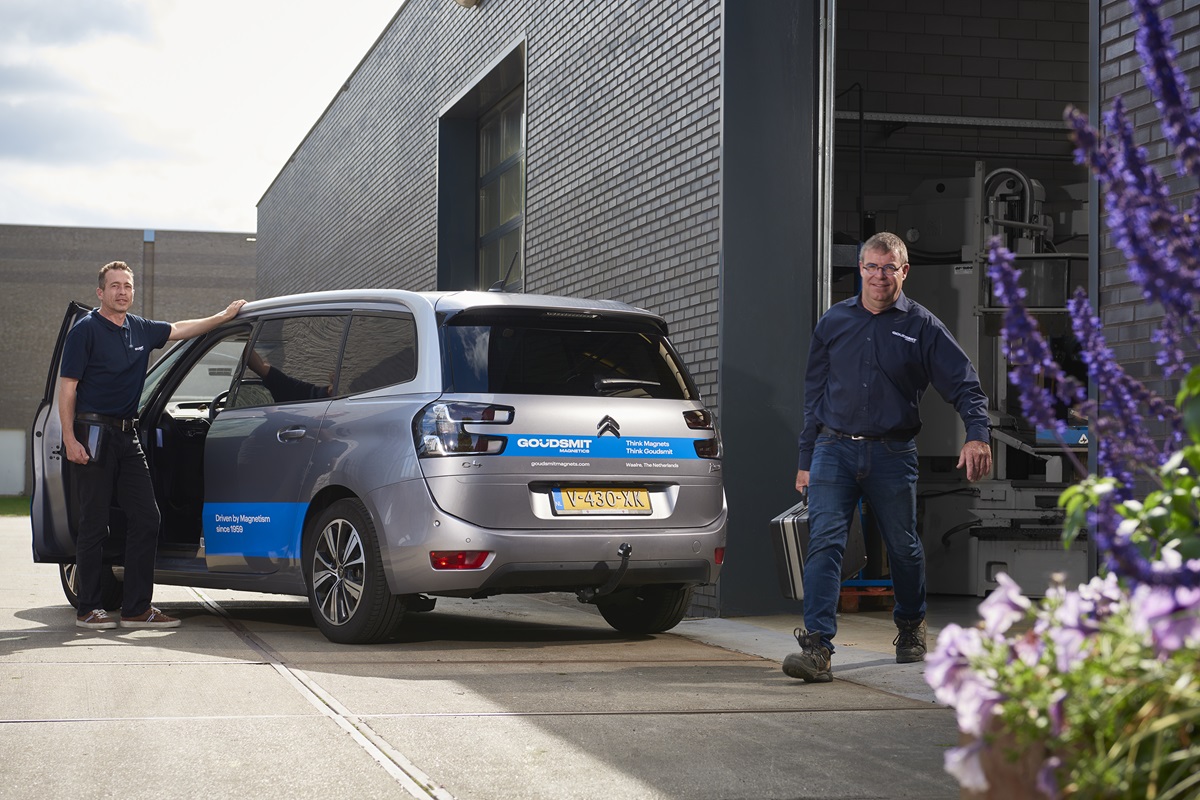
Field service engineers