Plastic & rubber
Our powerful magnetic separators separate even the smallest ferrous and non-ferrous metals. This gives you a metal-free plastic granulate that can be used as a secondary raw material.
Metal pollution in plastic and rubber granulate
There are many ways to collect plastic and rubber. Sometimes it is offered as a mono flow, but often as a mixed flow. Customers are setting increasingly strict requirements for the purity of processed plastic or rubber waste. Granulates may contain virtually no ferrous or non-ferrous contamination, in addition to foreign plastics. It is important to remove as much metal as possible, with the aim of: a pure plastic fraction that can be used as a secondary raw material.
It is also important that as little material as possible is lost. Current techniques such as sensor separators or metal detectors are not selective enough and separate too much – valuable – material. The right separators, in the right place in the process, help to find an optimum. But what do you then need?
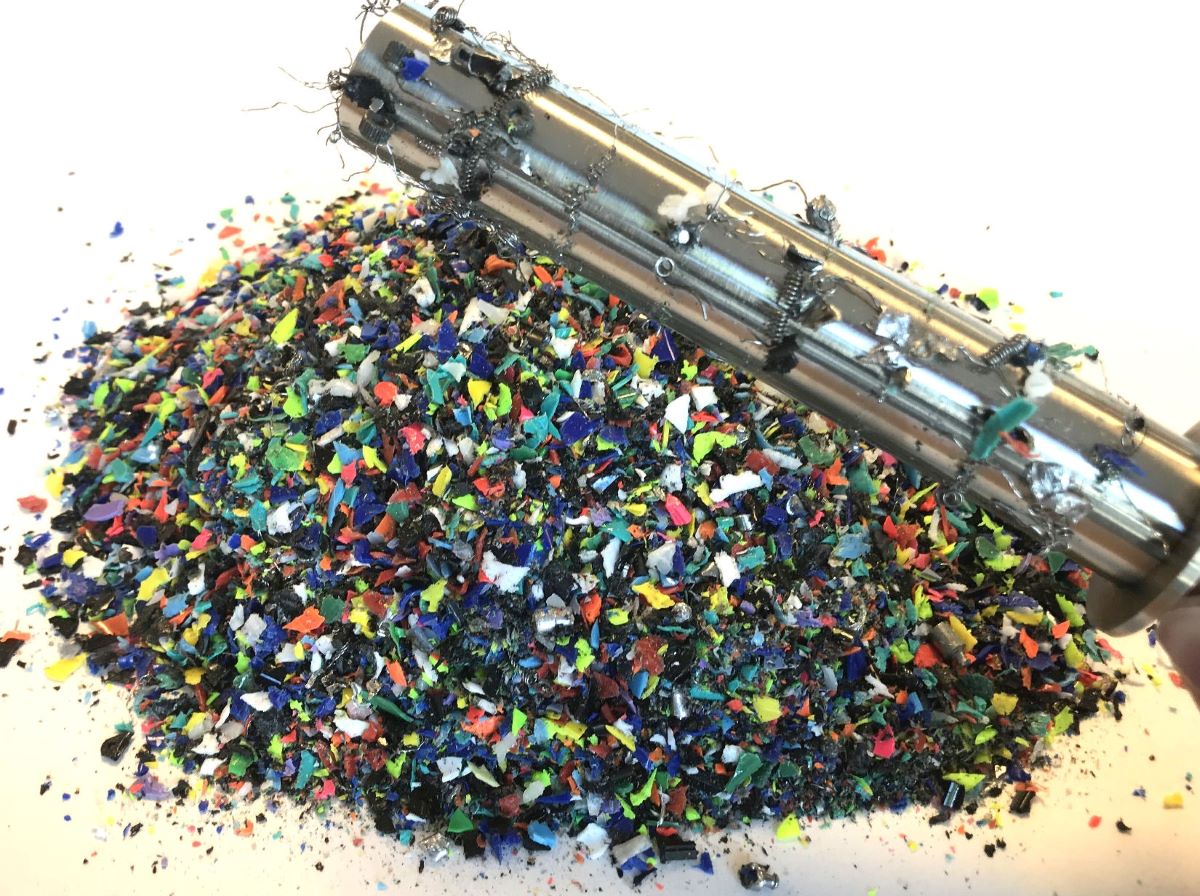
Magnetic separators for selective separation of coarse ferrous metals
Coarse and exposed ferrous metals larger than 1 mm can be easily separated from plastics with overband magnets. These are available with a permanent or electromagnetic field. In plastic or rubber processing, permanent magnets are usually preferred for reliability and cost-efficiency.
Overband magnets are easy to install above a conveyor belt and require little adjustment to your production line. That is why they are an ideal 1st separation step for getting plastic or rubber flows metal-free. With minimal product loss.
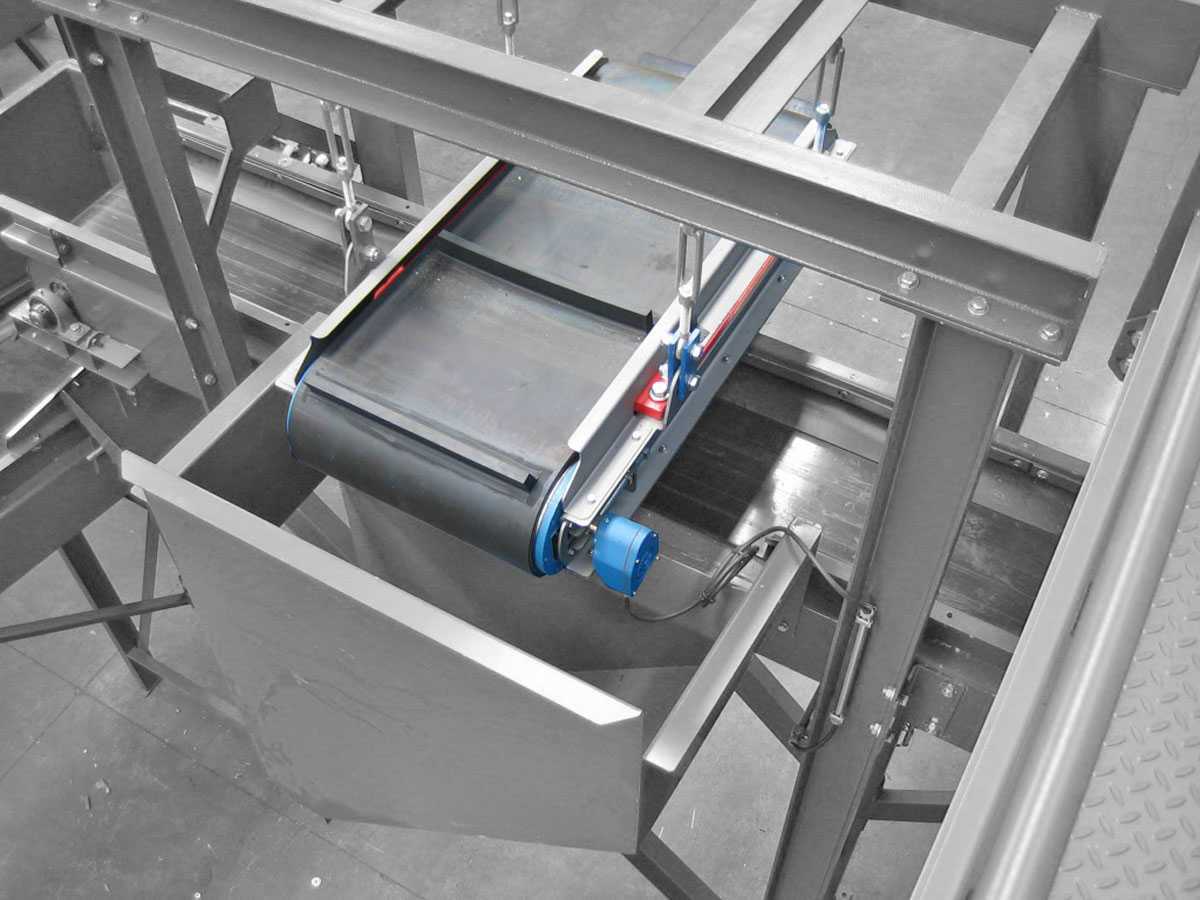
Separation of small encapsulated iron particles with high accuracy
Plastic flows contain many different iron particles. They mainly vary in composition, shape and thickness. The complexity of this mix determines the type of magnetic separator. Drum magnets and magnetic head pulleys provide very good deferrization from small or hard-to-separate parts, such as encapsulated iron.
Magnetic head pulleys are interchangeable, one-to-one, with a reversing roller in your existing line, but can also be purchased as a complete system. The latter gives you the ability to adjust settings such as layer thickness, belt speed and capacity, so that you always get the right purity.
Separate small iron and stainless steel parts with an extremely high magnetic force
Small, often round ferrous parts under 1 mm are difficult to separate. Just like stainless steel parts because they are only partly magnetic. Especially for these parts that are difficult to separate, there is the magnetic head pulley, fitted with a very strong 'high gradient' magnetic roller. This magnet system is so strong that it can even remove plastic or rubber particles that contain a small encapsulated ferrous particle.
This machine is often used in plastic recycling due to its compact construction, low-maintenance design and many setting options. The investment pays for itself quickly: the removal of stainless steel parts reduces the wear and tear of your expensive grinding mills or extruders.
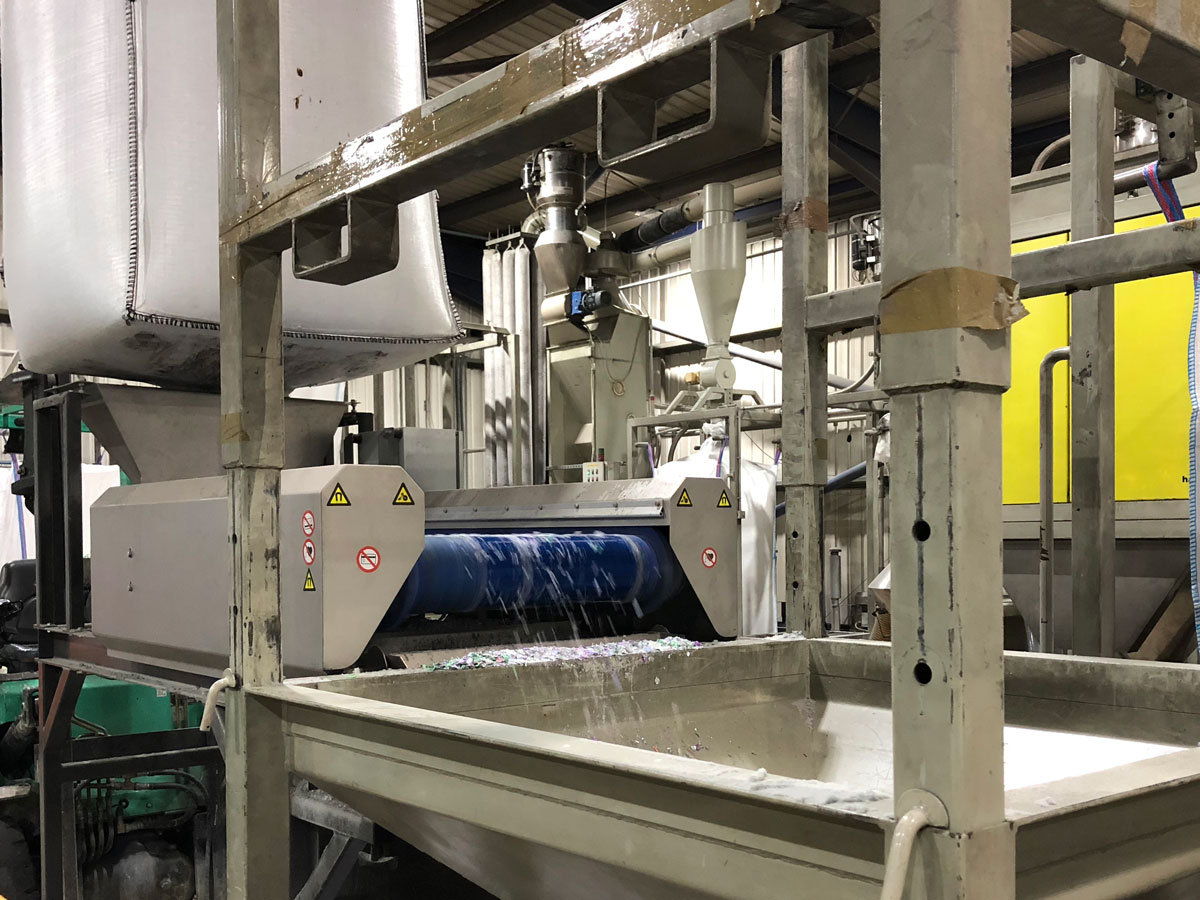
Removing non-ferrous metals with minimal material loss
Plastics recycling often uses eddy current separators because they can selectively remove non-ferrous metals. They only separate the encapsulated and free metals, unlike sensor separators and metal detectors. As a result, there is minimal loss of material and expensive pure plastic is retained.
With eddy current technology, you can separate non-ferrous metals as a metal mix from plastic and rubber. The metal mix consists, for example, of aluminium, copper, zinc, brass and stainless steel. It is crucial for you to remove these metals in order to use your plastic flow as a secondary raw material.
That is why there are 2 eddy current systems for processing plastic and rubber:
- 22HI EddyXpert: for plastic fractions of 5 - 20+ mm
- extra powerful 38HI EddyFines: for small particles between 0 - 10+ mm.
The following applies to eddy current separation:
- the drier the material, the more easily the metals can be separated
- the finer the fractions, the more difficult it is to remove the non-ferrous metals.
The purity of the final product is determined by:
- the shape of the plastic or rubber particles
- the desired volume per hour, and thus the layer thickness.
Custom advice: the right separator in the right place
We always strive for an optimal separation yield. By placing different magnetic solutions one behind the other. Or by combining different separation techniques, such as magnets in combination with metal detectors or electrostatic separators. If magnetic technology is not enough, we will also tell you.
Every material flow is different. Each process step ensures a cleaner final material. We have an extensive testing centre available to determine the properties of your material. Practical tests give a quick insight to select the right technique. After the analysis, we are happy to advise you so that you have the right separator in the right place. With an optimal separation yield.