Sheet metal industry
Magnet technology plays an important role in the reliable, safe and fast transport of steel sheets in various sizes. Our magnet systems ensure an efficient production process.
Challenges in the processing of sheet metal
Whether it concerns raw sheets, processed semi-finished products, perforated sheets or set products, the market is increasingly demanding more efficiency and accuracy, while costs must be reduced.
Safeguard profitability by preventing downtime
In order to produce profitably, a reliable, fast and accurate production environment is important. Downtime causes immediate losses and increases delivery times for your customers. That is why it is crucial to prevent downtime and damage to your production lines. Reliable and accurate machines have a direct impact on cycle times and thus on the profitability of your process. Determining the right tools and installations for your production process is therefore very important.
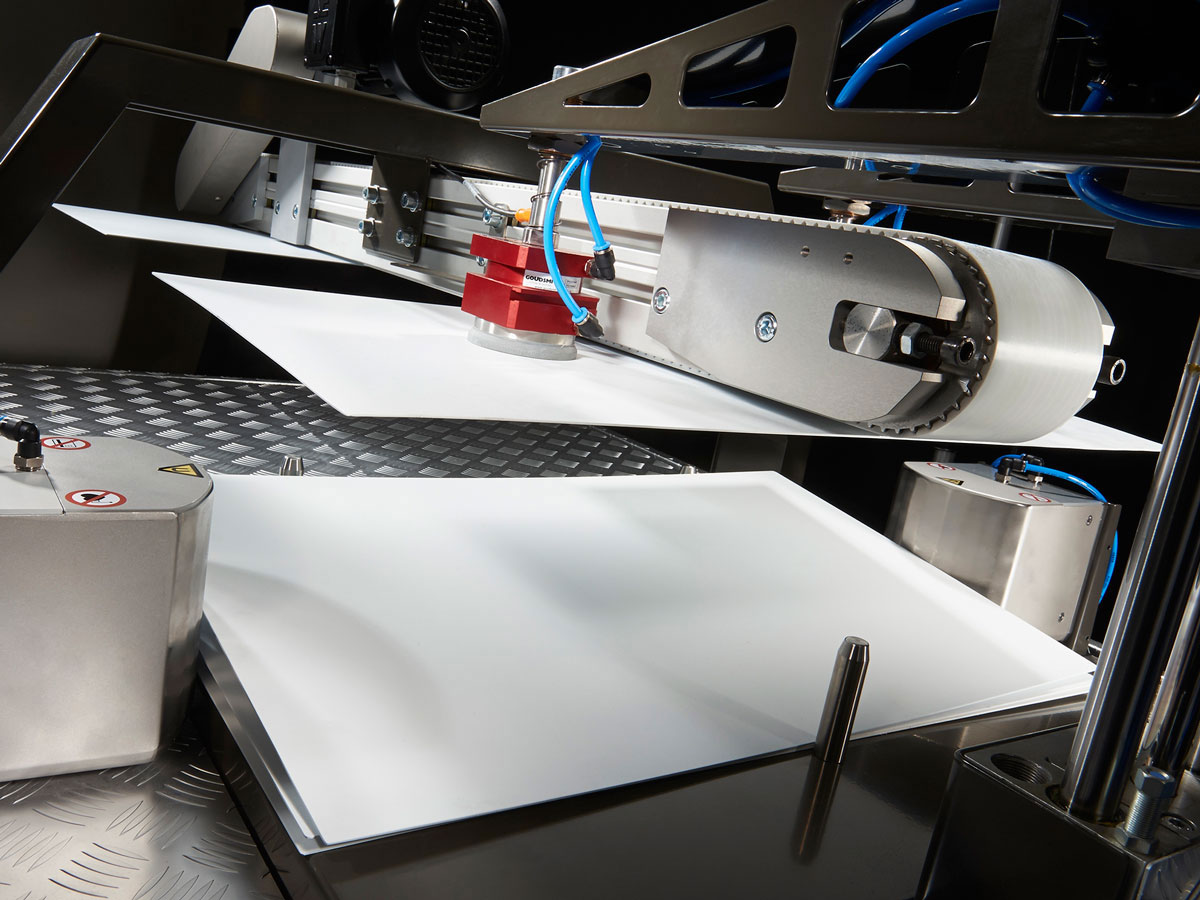
Magnetic timing belt with gripper and sheet separator for automatic sheet handling
Demand for shorter delivery times and automation
Manufacturers want an increasingly faster time-to-market. This requires increasingly shorter delivery times for semi-finished products. In order to realise these delivery times, automation is a requirement. Your manufacturing process needs to function more accurately and faster. Large runs, a lot of tolerances and less production time are challenges that play a continuous role. In order to remain competitive, it is necessary to invest in a production environment where this is possible.
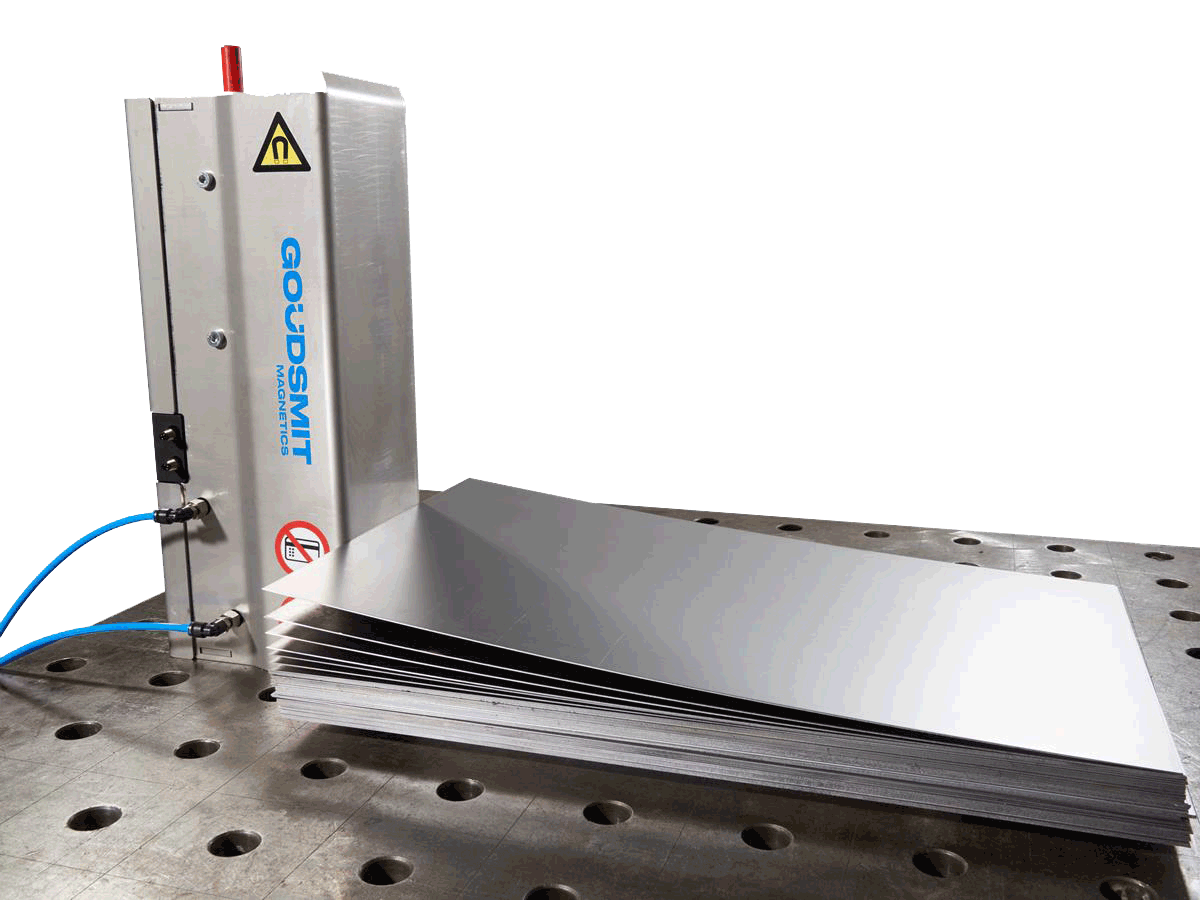
Sheet separator, pneumatic switchable
Loading errors due to increasingly thin sheet material
A trend in the production of sheet metal components is the increasing thinning of the starting material. This means that loading machines often pick up several steel sheets at once. This causes machine failure and line stoppage. That is why it is important to select suitable load tools for the sheet thicknesses in your production process.
Safety and sustainability for people and machinery
Safety is crucial in automated production lines. One accident can cause a chain reaction throughout the entire production process. Damage to people or machinery will then quickly result. The use of safe, user-friendly and reliable machines is therefore very important. Total cost of ownership is increasingly being taken into consideration. Energy use of your production processes plays a major role in this. To help the environment and minimise costs, it’s an extra challenge to select machines that consume little power and have a long service life.
We are happy to use our specialist skills to help you
Development, engineering and production take place at our head office in the Netherlands. Here, a team of engineers continuously works on the further development of our products, so that they can continue to meet market requirements. Through years of experience and intensive cooperation with our clients, we have developed a complete product programme that is suitable for the sheet metal industry. The use of magnets in your manufacturing processes offers many advantages. We are happy to advise you on the possibilities.
Magnets reduce production time and increase yield
Goudsmit’s magnets are specially designed to accurately position thin sheet material at high speed. This is possible thanks to balanced magnetic circuits and fast switching times. The use of magnets in your production line immediately saves time and results in significant savings on your total production time.
Pneumatically switched magnetic grippers hold flat ferromagnetic objects, such as steel sheets, firmly in their grip, even if the air pressure drops.
Shorter delivery times due to automated production processes
Magnets enable you to further automate your production process and reduce cycle times. Our engineers design these magnet systems with automation as their starting point. Among other things, they provide possibilities for sensors, detection and reading. This makes it possible to have magnets communicate with BUS systems, for example. Magnets are therefore an integral part of your production line; a component whose status is always known.
Safer and more energy efficient process thanks to magnet technology
Goudsmit’s magnet systems are developed in such a way that safety during use is guaranteed. For example, a magnet holds the product permanently, even when air pressure is interrupted. Other techniques based on vacuum or overpressure do not have these advantages. In addition, all Goudsmit magnets are CE-marked, which meets the European safety standards. The low energy consumption is a unique additional benefit. Permanent magnets are always ‘on’. By making smart use of this, they are very energy efficient. Instead of a continuous supply of power or compressed air control, most magnets can be operated with a single pulse of air pressure. This amounts to a fraction of the continuous energy costs.
Fast delivery times and global service
If your process line fails or you want to implement an optimisation quickly, you will immediately look for a solution. That is why Goudsmit has so many products and spare parts in stock. You can see the current stock and delivery time on our website.
For the installation of spare parts or for maintenance to your magnets, you can always contact our service department. Professional service engineers resolve malfunctions or downtimes of magnets quickly, safely and effectively.