Pneumatic magnetic grippers
Search results
Your results in: pages, products and documents
Scroll to see everything. Didn't find what you were looking for?
Try another search term or contact us.
-
{{filter.Description}}
({{filter.UOMDescription}})
No results found
Your results in: pages, products and documents
Scroll to see everything. Didn't find what you were looking for?
Try another search term or contact us.
Application of magnetic End of arm tooling
Pneumatic magnetic grippers are ideal when you want to handle flat steel products. Automated production and assembly lines in particular are equipped with magnetic grippers. For example in machines, or as an end effector for robots. They load/unload, lift and position workpieces in CNC machines, folding machines, press brakes, punching machines or bending, laser cutting and welding cells.
Compressed air moves the magnetic core in the pneumatic gripper, effectively turning the magnetic field on or off. In this way, workpieces remain firmly in place, even in the event of a power failure. They also easily hold perforated plates.
The high-temperature magnetic grippers operate reliably in environments up to 120°C. Application examples for the high-temperature grippers are bakeries, press brakes and automotive assembly lines.
Connection and operation of the magnetic gripper
The magnetic gripper switches pneumatically. You can control the air flow with a 5/3 or possibly a 5/2 valve. Goudsmit pneumatic grippers can be equipped with sensors for on/off detection and product presence detection. Other accessories include spring plungers for extra damping.
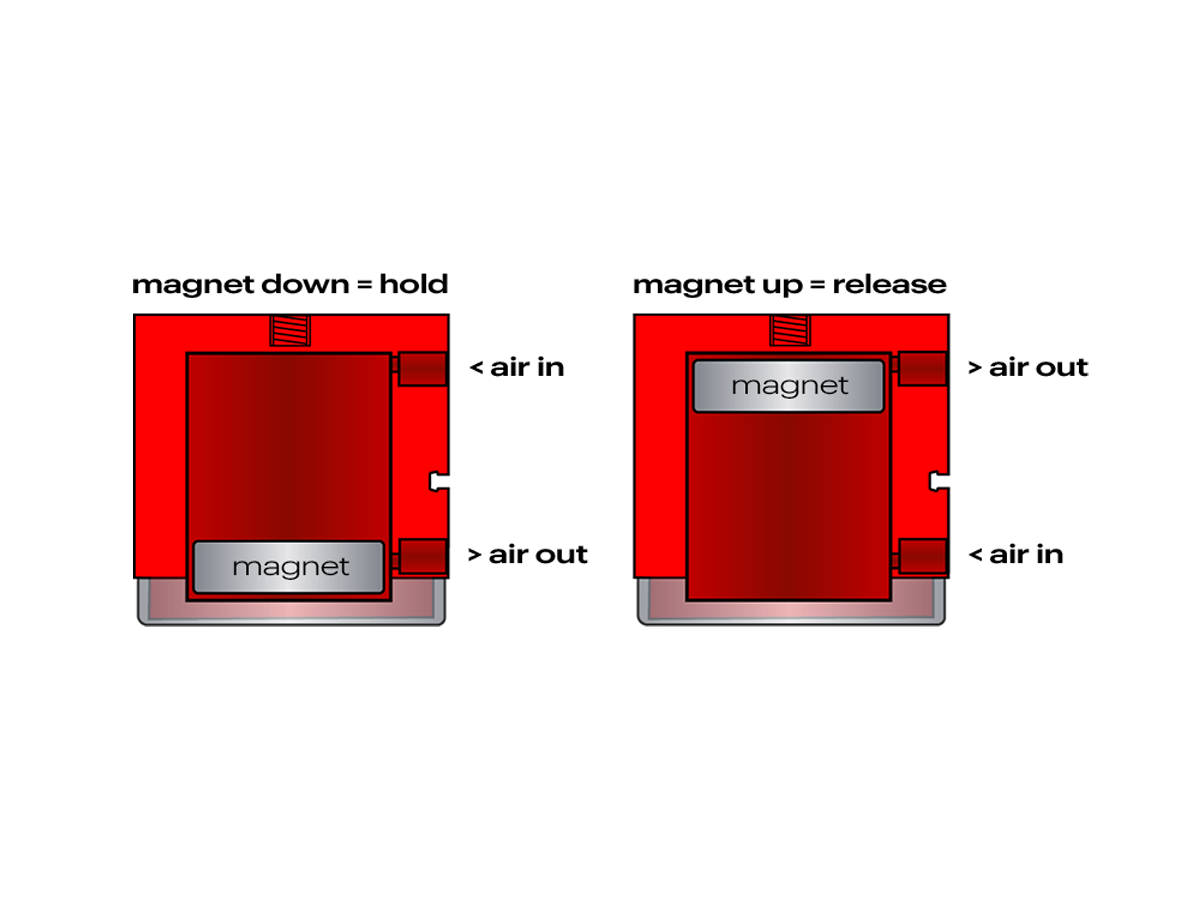
Factors affecting magnetic lifting force
Pneumatic grippers are designed to handle ferromagnetic products and workpieces. The achievable holding force depends on the magnetic properties and the chemical composition of the material to be handled. Compared to low-carbon steel, the holding force of magnetic grippers may be lower with other materials:
Material / Efficiency
- Non-alloy low-carbon steel (<0.3% C) such as Fe 360 Fe 510: 100%
- Non-alloy carbon steel (0.3 – 0.5% C) such as C15, C45: 80 - 90%
- High-carbon (0.5 – 1.8% C) alloy tool steel: 70 - 80%
- Magnetic stainless steel (ferritic, martensitic) such as AISI430: 60 - 75%
- Cast iron (>1.8% C): 45 - 50%
- Nickel: 30 - 50%
- Stainless steel AISI304: 1 - 3%
- Austenitic stainless steel such as AISI316, brass, aluminium, copper: 0%
In addition to the workpiece material, these factors also reduce the holding force:
- An air gap between the workpiece and gripper. Non-magnetic surface layers such as coatings, foil, rust, dirt, but also rough surfaces lead to an air gap and reduce the holding force.
- Contact surface. When the workpiece is in full contact with the magnetic poles, the maximum holding force is reached. With partial coverage or reduced contact, for example because the workpiece is perforated or hard to touch, the holding force decreases.
- The thickness of the workpiece. When working with thin plates (≤1 mm), take the 'peeling effect' into account. This reduces the maximum breakaway force. In this situation, it is better to make a construction with several smaller grippers (for example 40 mm) than one or two large grippers.
- Temperature. Both a higher ambient temperature (>30°C) and a higher product temperature (40 - 80°C) reduce the magnetic force. The high-temperature grippers are more resistant to these effects.
- Acceleration forces. When the workpiece moves quickly, acceleration forces can negatively affect the holding force. Always ensure that the acceleration forces on the workpiece are significantly lower than the holding force.
- Stiffness or flexibility of the load. Long or flexible loads can sag. The deflection effect on the magnet significantly reduces the holding force. Provide enough magnetic grippers at multiple gripping points to prevent sagging. Also provide a flexible suspension of the magnetic grippers to absorb the deflection.
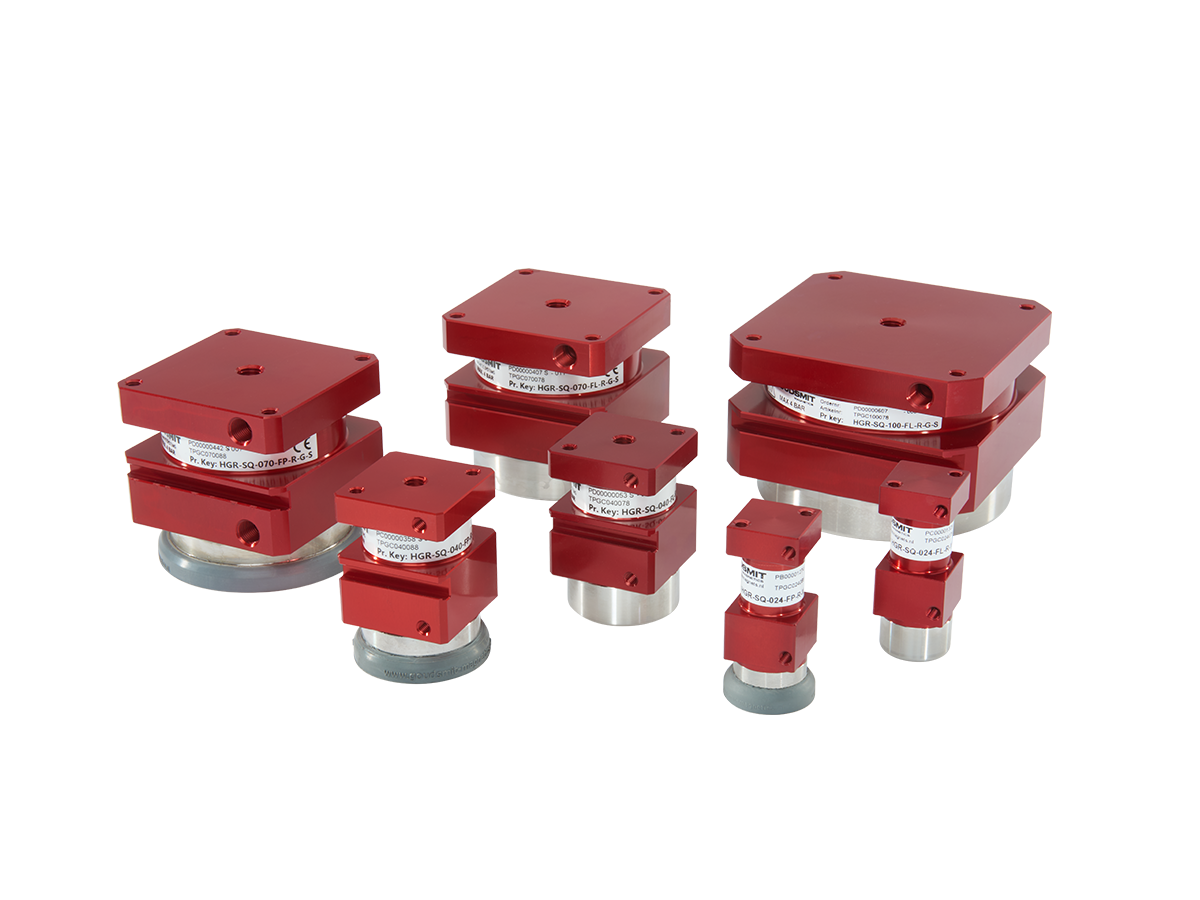
Pneumatic magnetic grippers allow you to safely handle steel workpieces and plates with great speed and precision. Grippers – also known as end effectors – are ideal for speeding up or automating your production process. Durable, safe and accurate robot grippers are a reliable end of arm solution due to the bistable design.