Recycling industry
The recovery of metals from waste for reuse, among other purposes, is becoming increasingly important. Raw materials are becoming scarcer and the costs of dumping waste continue to rise. This results in increased market demand for the recycling of metals from waste.
Challenges in recycling
The demand for secondary raw materials or recycled materials is increasing. The joint climate objectives and the pursuit of a circular economy emphasise this. As a manufacturer, you want to respond to this need and thus meet the material requirements that are required for recycled product flows.
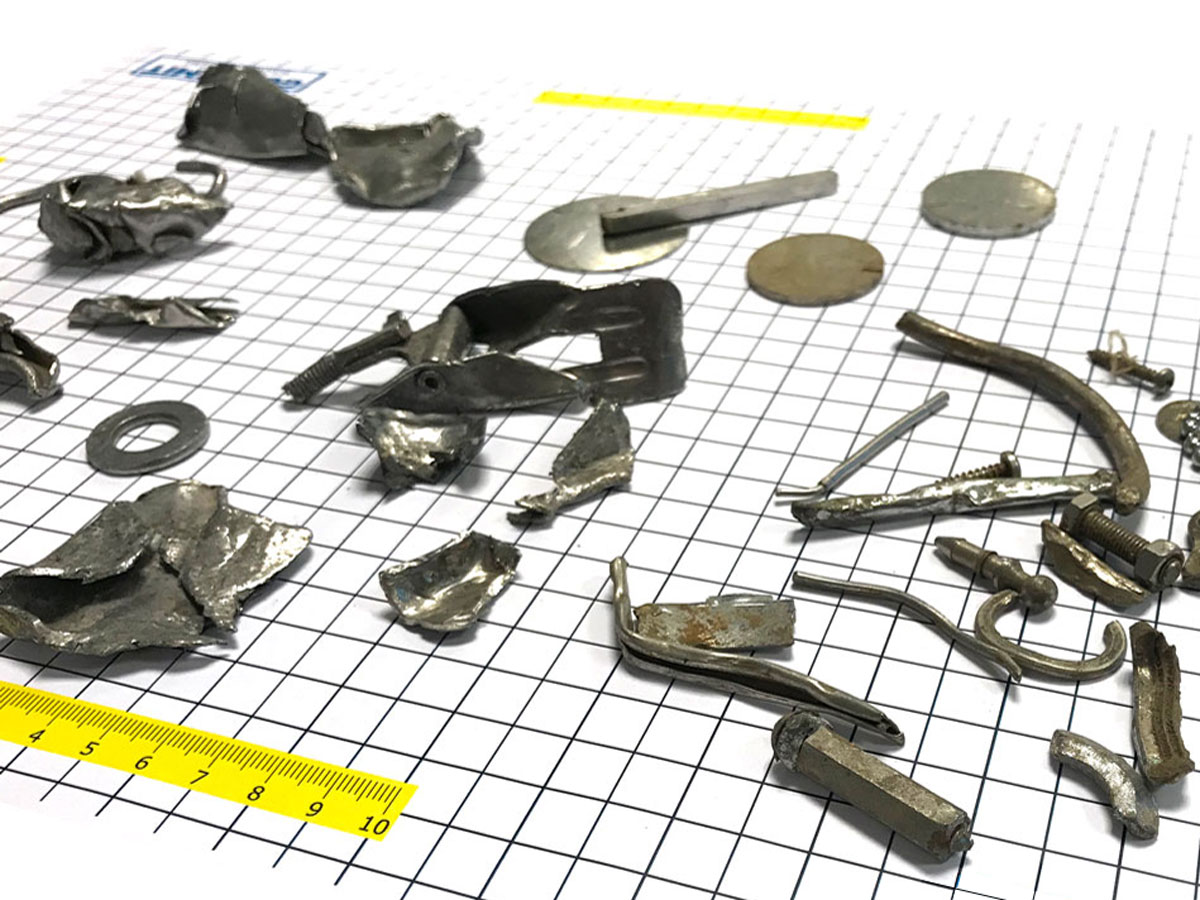
Saleable fraction with magnetic separator
Which magnetic separator produces a saleable fraction?
One of the biggest challenges in the recycling industry is converting mixed product flows into pure fractions that are ready for reuse. Constantly changing compositions, the influence of environmental conditions and varying input qualities make it difficult to create continuously marketable fractions. A small percentage of contamination can have a major impact on the yield of your secondary raw materials. Whether you want a metal-free plastic flow or a marketable non-ferrous metal mix, the pure separation of metals remains a challenge. Magnetic separators provide a solution for strongly magnetic, weakly magnetic or non-ferrous metals. But it requires a lot of knowledge to select the right machine for your specific separation issue.
Uptime and service life crucial for yield
To create sufficient margin, it is important to produce as much material as possible, where costs per tonne are crucial. One driving factor is the uptime and service life of the machines in your production line. A machine that often fails or requires a lot of maintenance causes higher costs per tonne. In addition, you want a machine that is easy to operate so that every operator gets the best results.
Accidents during operation or maintenance
Safety is an important topic in recycling. Many product streams are flammable and can catch fire due to, for example, a machine producing sparks or a hot bearing. Machines can also cause dangerous situations for operators. Especially if they are not easy to maintain. In this case, a quick solution is often chosen that leads to accidents or problems.
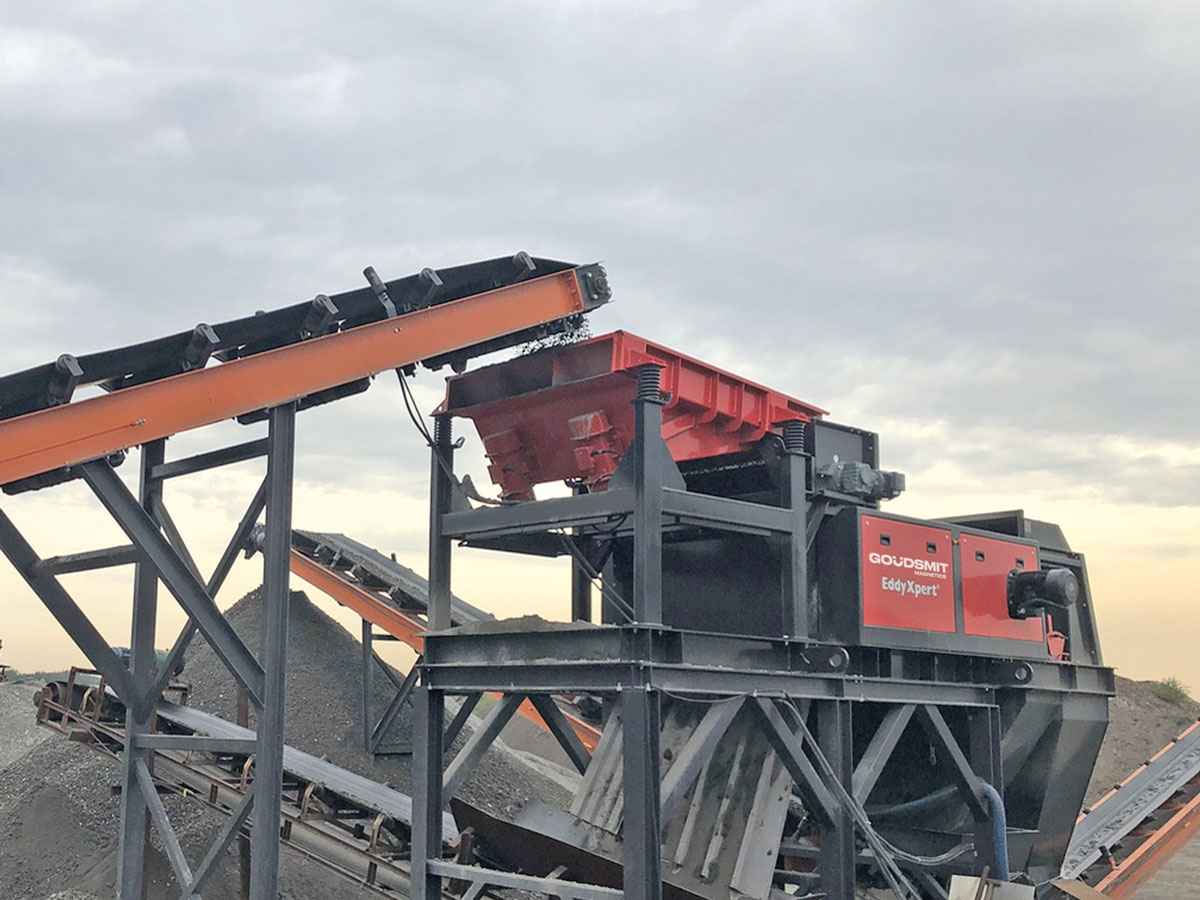
Mobile magnetic separator for ferrous and non-ferrous metals
We are happy to use our specialist skills to help you
Goudsmit develops magnet systems for separating the complete range of metals from waste. Through thousands of practical tests we know what works and what doesn’t. With our knowledge and expertise in the field of magnetic separation, we are happy to advise you on the possibilities.
Test centre for customised advice
Processing product flows is costly. That is why we get the maximum value from your product together with you. Investments in machines are focused on the long term. You want to see the yield for your specific material. That is why we have set up a test centre especially for the recycling sector. With a complete set-up of magnetic separators, including eddy current separators with vibratory feeders, drum magnets, head pulley separators, overband magnet separators and combinations of these systems. This allows our experts to test bulk samples of all your materials, from coarse to very fine. This allows us to gain insight into the possibilities quickly and you will know whether investments are profitable.
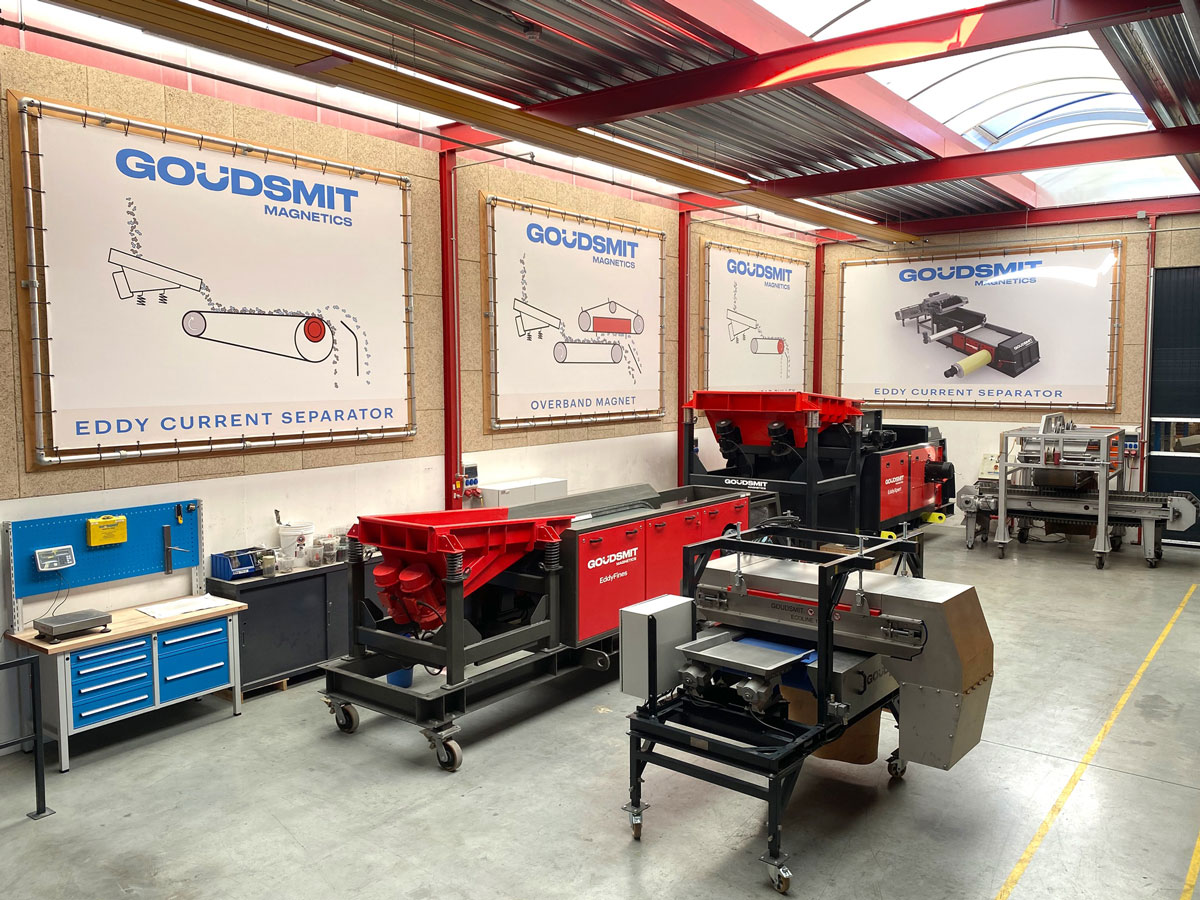
Test centre for all magnets and magnetic systems
Separating strongly magnetic metals
Strongly magnetic metals are the easiest to separate. Separators such as magnetic pulleys, drum and overband magnetic separators remove continuous ferrous metals such as iron and steel. We are happy to advise you on the different magnet systems, each of which serves its own unique purpose on a process line.
Separating weakly magnetic metals
We also produce magnetic separators for removing weakly magnetic metals, such as stainless steel and other steel alloys from waste flows. Goudsmit is distinguished in the area of high-gradient magnet systems. These extremely powerful machines are unrivalled and make it possible to efficiently separate weakly magnetic metals or very small particles. These separation steps are more difficult than those of strongly magnetic separation. We are happy to help you optimise your process.
Separating non-ferrous metals
Eddy current separators separate non-ferrous metals such as aluminium and copper from bulk streams. This separation step is the most complex, especially with the smallest particles. But the yield is therefore highest. To achieve the desired separation yield, we offer you the most powerful magnet technology available on the market. The combination of the best technology and custom advice turns your separation issue into a profitable overall concept.
The Eddy current separator with drum magnet separates steel parts (ferrous fractions) as well as aluminium, copper, brass and other metals (non-ferrous) from plastics.
High uptime through quality and practical knowledge
Our engineers design magnetic separators with simplicity of use and maintenance as a starting point. This minimises emergencies and downtime. All Goudsmit machines therefore have European CE certification and comply with machine guidelines. As a company, we are also certified to issue ATEX-labelled machines. In this way, we can help you with a process line in an explosive environment.
By working closely with our customers, we design robust and continuously performing machines that generate a high yield. Through practical experience, we know which parts wear out fastest. We use high-quality materials and parts to minimise wear and failure and extend lifespan. By applying quality in both construction and components, many machines have been running for more than 20 years.
Fast service and after-sales to get you up and running again
The machines in your production line need maintenance from time to time. When a part is worn out, you want to run production again quickly. The Goudsmit service department can provide help quickly. Most spare and wear parts are in stock in our warehouse and can be delivered quickly. You may choose to have the parts installed by your own technical service or by one of our specialist service engineers.