Special demagnetizing tunnel for Pioneering Spirit
12-metre tubes that need to be welded together to 24 metres and form a pipeline in the sea through which - in this case - gas flows is quite a job, but is daily business for Pioneering Spirit. The largest construction vessel in the world is owned by Swiss-Dutch offshore contractor Allseas and is located off the coast of Rotterdam, at the Maasvlakte. Her job is to install and remove rotary offshore platforms and lay the largest and heaviest undersea pipelines on the seabed. The colossus is 477 metres long, 124 metres wide and can handle 48000 tonnes. It picks up a drilling rig in just 10 seconds. Incredible but true.
Problem: residual magnetism obstructs pipeline welding
To lay pipelines, an on-board factory welds together pipe sections, which are lowered onto the seabed. During the welding process, Pioneering Spirit engineers thought of an opportunity to improve the welding process, for which they called in Goudsmit Magnetics. Almost all ferrous metals can contain residual magnetism; so did some of the pipe segments in Pioneering Spirit that could not be welded together so easily. This is because the arc contains electrons, causing it to deflect because of the magnetic field. As a result, there is a chance of an inferior weld that may not pass the strict quality controls. Two of our engineers travelled to the Maasvlakte to investigate whether the improvement could be implemented in the process. They took a gaussmeter and a number of demagnetizing systems with them, including a demagnetizing tunnel and a mobile demagnetizing unit.
Special custom-made demagnetization tunnel
After a day of testing, the demagnetization tunnel proved to give the desired result. But in the offshore industry, corrosion resistance is always a challenge, so we were asked if it was possible to make a special, extra robust tunnel with a housing made of plastic. Preferably a precise fit, leaving as little air gap as possible between pipe and tunnel. We succeeded. For mounting to the ship, a frame made of non-magnetic stainless steel sits on the tunnel. Based on the result from the first field test, our FEM Engineers calculated the correct sizing of design parameters. Based on this, mechanical engineers then took care of mechanical elaboration of the demagnetization tunnel. This resulted in the most optimal design for Pioneering Spirit's application.
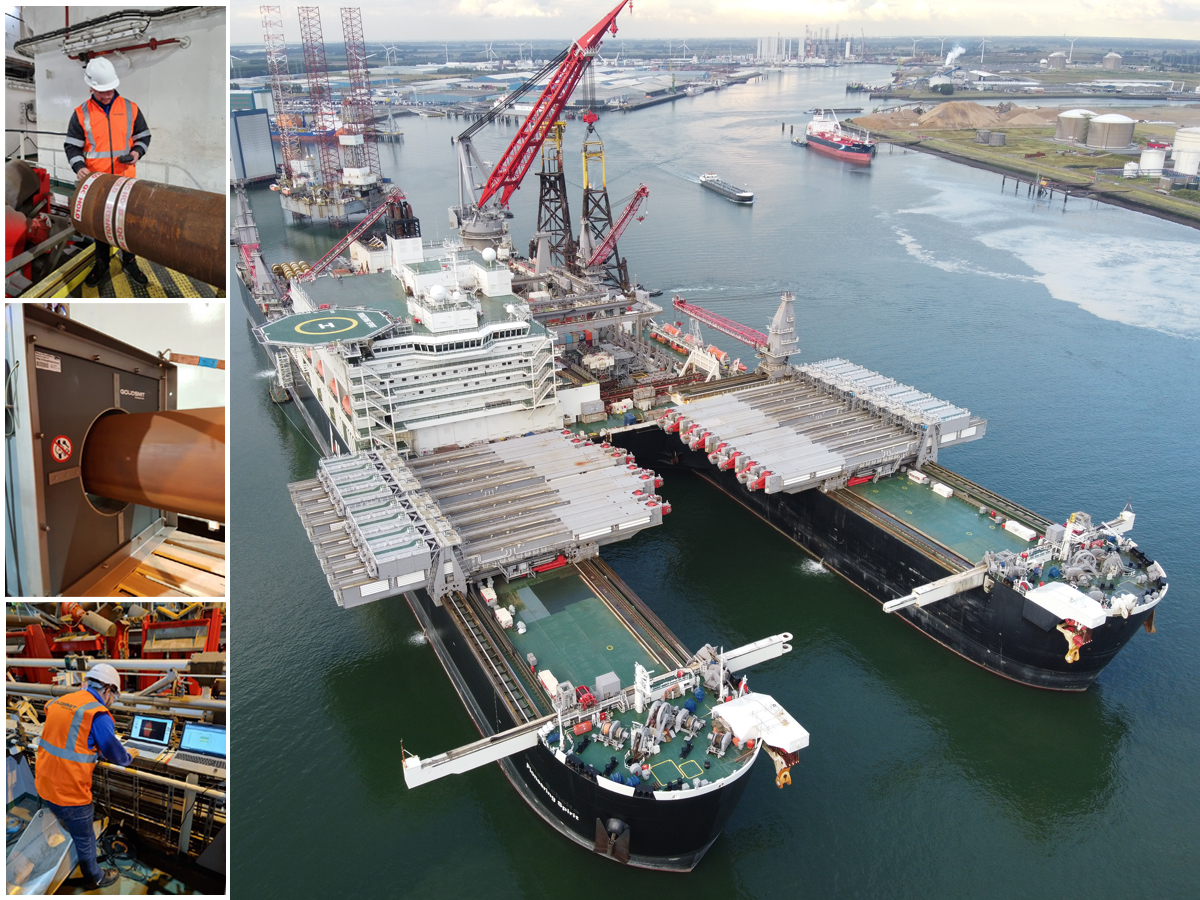
Special control box and on-site commissioning prove successful
The standard control system was also modified upon request. The Pioneering Spirit team wanted a start/stop sensor, which makes the through tube turn on and off the tunnel. The tubes are made of a thick steel alloy that can hold more magnetism. If there is more magnetic field, you also need more current to extract the magnetism. Demagnetization is possible by creating a decreasing alternating magnetic field in the work piece. This is achieved with an alternating continuous signal and passage of the product through the tunnel. The lower the frequency, the deeper the signal penetrates the metal. But low frequency also requires low pipeline throughput through the tunnel. The limitation of our system is the frequency and for the client it is the speed of the pipe to be installed.
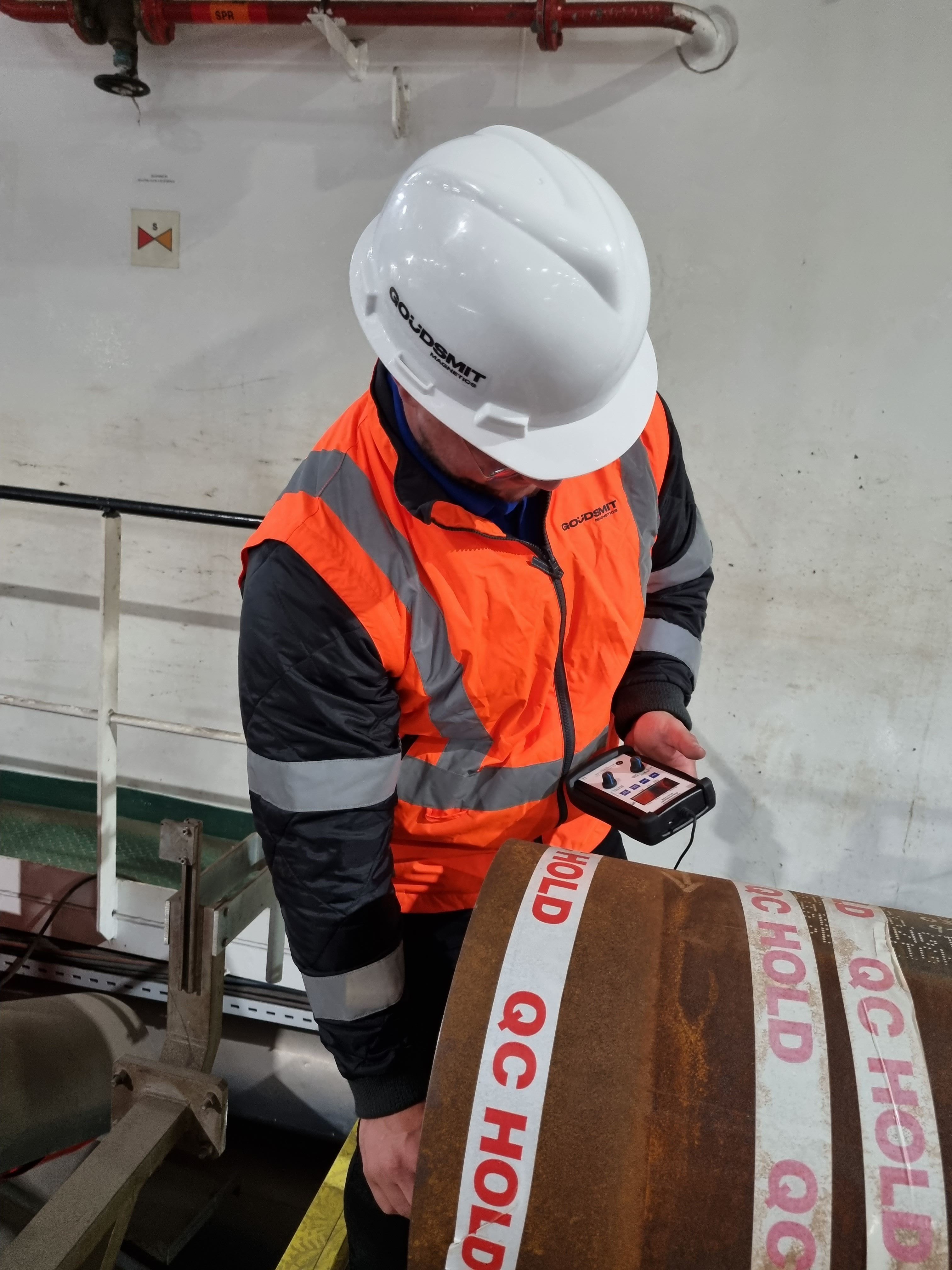
During commissioning of this customer-specific demagnetization system, we searched for the optimum between throughput, frequency, current and pure signal shape. By targeted testing in a number of iterations, we achieved the best result and were able to optimally tune the controller to the client's product on site.
A suitable solution for every process
The tubes are delivered on a kind of powered roller conveyor system and with the help of this system it is possible to demagnetise with a continuous signal while the tube moves through the tunnel. Depending on the application, there are 3 possibilities for demagnetisation. With a decreasing signal, with a continuous signal or with a constant signal. The less the tunnel is on, the less it gets hot or consumes energy. In half an hour, two tubes are demagnetised and then welded together to form a 'joint'. This process continues 24 hours a day. Even though magnetism is desirable in nine out of 10 cases; unwanted magnetism can hinder a lot of processes. But Goudsmit has a solution for that too!